Heat stabilizer for producing PVA product and method for producing PVA product
A technology of heat stabilizer and stabilizer, which is applied in the direction of flat products, applications, household appliances, etc., and can solve problems such as non-continuous production
- Summary
- Abstract
- Description
- Claims
- Application Information
AI Technical Summary
Problems solved by technology
Method used
Image
Examples
Embodiment 1
[0085] 100 parts of 1788 polyvinyl alcohol, 10 parts of sorbitol, 5 parts of acrylamide, 0.02 parts of calcium hydroxide, 0.02 parts of calcium sulfate, 1 part of nano hydrotalcite, 2 parts of AO-13, 0.5 parts of AO-28, 1 part DSTP, 1 part of pentaerythritol tetrastearate, 0.3 parts of zinc stearate were mixed at 30°C-80°C for 30-50 minutes, extruded and granulated in a twin-screw extruder at 200-240°C, and the above pellets were mixed in a single The film is blown at 230-240° C. under 30-50% relative humidity in a screw extruder to obtain a thickness of 30-45 μm, and the film ruptures and dissolves at 25° C. for 35S. The torque of the pellets after banburying is as follows: Figure 5 As shown in curve 2, after the heat stabilizer is added, the corresponding torque rise rate gradually decreases, and the torque rise rate represents the increase rate of the viscosity of the melt system, which can represent the speed of PVA thermal aging rate. The decrease in the torque rise rat...
Embodiment 2
[0087] 100 parts of 1799 polyvinyl alcohol, 10 parts of polyethylene glycol, 10 parts of acrylamide, 15 parts of ethylene glycol, 0.5 parts of calcium hydroxide, 0.01 parts of copper phosphate, 3 parts of nano china clay, 1 part of AO-16, 0.3 parts AO-28, 0.5 part of TNP, 0.5 part of glyceryl monooleate, 3 parts of dibasic lead stearate were mixed at 50-100°C for 40-80 minutes, and extruded in a twin-screw extruder at 200-250°C pellets, blow the above pellets into a film at 200-250°C in a single-screw extruder at a relative humidity of 30-50%, to obtain a thickness of 70-80 μm, the film is insoluble in deionized water at 25-35°C, and is 60-80 ℃ deionized water 15-60S rupture and dissolve.
Embodiment 3
[0089] 100 parts of 1799 polyvinyl alcohol, 30 parts of sorbitol, 10 parts of acrylamide, 5 parts of oleic acid amide, 0.002 parts of magnesium hydroxide, 0.01 parts of copper phosphate, 0.5 parts of DSTP, 2 parts of nano china clay, 2 parts of AO-1, 0.2 parts of AO-5, 0.3 parts of AO-31, 0.5 parts of TPP, 0.5 parts of glyceryl monooleate, 0.2 parts of dibasic lead stearate, 0.5 parts of tridecyl stearate were mixed at 150°C for 30 minutes, Extrude and granulate at 180-250°C in a twin-screw extruder, and the torque of the pellets after banburying is as follows: Figure 5 As shown in curve 3, after the heat stabilizer is added, the corresponding torque rise rate gradually decreases, and the heat stability increases. Blow the above pellets into a film at 200-250°C in a single-screw extruder at a relative humidity of 50% to obtain a thickness of 70-80 μm, which is insoluble in deionized water at 25°C and deionized at 50-80°C 15S-150S breaks and dissolves in water.
PUM
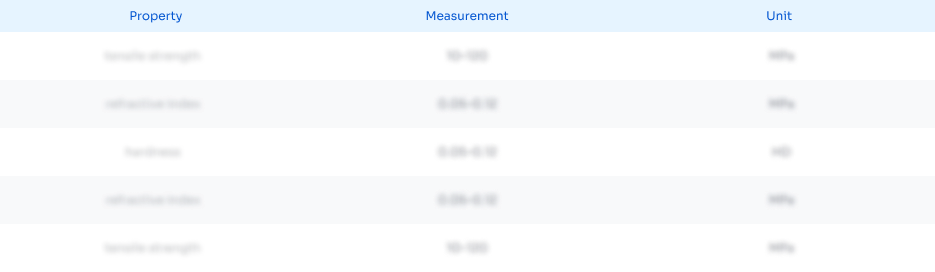
Abstract
Description
Claims
Application Information

- R&D
- Intellectual Property
- Life Sciences
- Materials
- Tech Scout
- Unparalleled Data Quality
- Higher Quality Content
- 60% Fewer Hallucinations
Browse by: Latest US Patents, China's latest patents, Technical Efficacy Thesaurus, Application Domain, Technology Topic, Popular Technical Reports.
© 2025 PatSnap. All rights reserved.Legal|Privacy policy|Modern Slavery Act Transparency Statement|Sitemap|About US| Contact US: help@patsnap.com