Continuous compensating method of displacement precision of digital controlled shaft of digital controlled machine tool
A technology of numerical control machine tools and compensation methods, which is applied in the direction of automatic control devices, metal processing machinery parts, feeding devices, etc., and can solve the problems of difficulty in restoring the accuracy of machine tools, errors, unfavorable maintenance of machine tools, etc.
- Summary
- Abstract
- Description
- Claims
- Application Information
AI Technical Summary
Problems solved by technology
Method used
Image
Examples
Embodiment Construction
[0062] Below in conjunction with the accompanying drawings and preferred embodiments, the specific implementation, structure, features and effects of a method for continuously compensating the displacement accuracy of the numerical control axis of a numerical control machine tool according to the present invention will be described in detail as follows.
[0063] A method for continuously compensating the displacement accuracy of a numerical control axis of a numerical control machine tool, comprising the following steps:
[0064] (1) Set a reference point 0 at the middle position within the effective stroke range of the CNC axis, divide the effective stroke of the CNC axis into a number of equal line segments with a length of A with the reference point as the origin, and divide the effective stroke of the CNC axis into For positive segmentation and negative segmentation, the positive segmentation point is marked as p (p=1, 2, 3, 4, 5, ...); the negative segmentation point is ma...
PUM
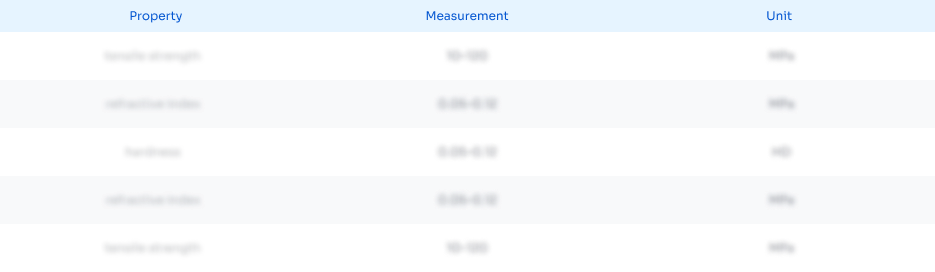
Abstract
Description
Claims
Application Information

- R&D
- Intellectual Property
- Life Sciences
- Materials
- Tech Scout
- Unparalleled Data Quality
- Higher Quality Content
- 60% Fewer Hallucinations
Browse by: Latest US Patents, China's latest patents, Technical Efficacy Thesaurus, Application Domain, Technology Topic, Popular Technical Reports.
© 2025 PatSnap. All rights reserved.Legal|Privacy policy|Modern Slavery Act Transparency Statement|Sitemap|About US| Contact US: help@patsnap.com