Preparation method of bulk myclobutanil
A technology of myclobutanil and the original drug, applied in the field of preparation of myclobutanil original drug, can solve the problems of low purity, limited product yield, high production cost, etc.
- Summary
- Abstract
- Description
- Claims
- Application Information
AI Technical Summary
Problems solved by technology
Method used
Image
Examples
Embodiment 1
[0016] Embodiment 1: the production of the original drug of myclobutanil mainly consists of the following steps:
[0017] One.1,2-(4-chlorophenyl) hexonitrile production: drop into p-chloronitrile benzyl, chlorinated n-butane, phase transfer catalyst tetrapropyl ammonium bromide successively in reactor (being chloronitrile benzyl weight 4 -6%, the same below), the temperature of the reactor is controlled at 55° C., and the mass concentration is slowly added dropwise to 50% sodium hydroxide solution, and the chlorinated benzyl: n-chlorobutane: the mol ratio of sodium hydroxide is controlled At 1: 1.2: 1.3, the dropping time is controlled at 3 hours. After the liquid caustic soda is dripped, the temperature is raised to 78°C to start timing and heat preservation. Wash with toluene and deionized water whose weight is 1 times the weight of n-chlorobutane, then let it stand and remove the lower wastewater in the reaction kettle, then feed in deionized water to wash the reaction pro...
Embodiment 2
[0020] Embodiment 2: the production of the original drug of myclobutanil mainly consists of the following steps:
[0021] One.1,2-(4-chlorophenyl) hexonitrile production: drop into p-chloronitrile benzyl, chlorinated n-butane, phase transfer catalyst tetrapropyl ammonium bromide successively in reactor (being chloronitrile benzyl weight 4 -6%, the same below), the reaction kettle temperature is controlled at 60 ℃, slowly dripping mass concentration is 50% sodium hydroxide solution, described p-chloronitrile benzyl: chlorobutane: the mol ratio control of sodium hydroxide At 1:1.4:1.5, the dropping time is controlled at 2 hours. After the liquid caustic soda is dripped, the temperature is raised to 77°C to start timing and heat preservation. Toluene and deionized water with a weight of 1.2 times the weight of n-chlorinated butane were washed, then left to stand and the lower layer of wastewater in the reactor was removed, and deionized water was added to wash the reaction produc...
Embodiment 3
[0024] Embodiment 3: the production of the original drug of myclobutanil mainly consists of the following steps:
[0025] -.1,2-(4-chlorophenyl) hexonitrile production: drop into p-chloronitrile benzyl, chlorinated n-butane, phase transfer catalyst tetrapropyl ammonium bromide successively in reactor (being chloronitrile benzyl weight 4 -6%, the same below), the reaction kettle temperature is controlled at 65 ℃, and slowly dripping mass concentration is 50% sodium hydroxide solution, and described p-chloronitrile benzyl: chlorobutane: the mol ratio control of sodium hydroxide At 1:1.6:1.7, the dropping time is controlled at 3 hours. After the drop of liquid caustic soda is completed, the temperature is raised to 75°C and the time insulation is started. Toluene and deionized water with a weight of 1.3 times the weight of n-chlorinated butane were washed, then left to stand and removed the lower wastewater in the reactor, and then fed into deionized water to wash the reaction pr...
PUM
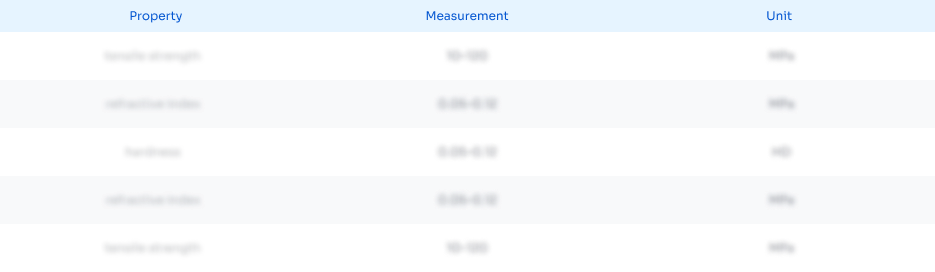
Abstract
Description
Claims
Application Information

- R&D Engineer
- R&D Manager
- IP Professional
- Industry Leading Data Capabilities
- Powerful AI technology
- Patent DNA Extraction
Browse by: Latest US Patents, China's latest patents, Technical Efficacy Thesaurus, Application Domain, Technology Topic, Popular Technical Reports.
© 2024 PatSnap. All rights reserved.Legal|Privacy policy|Modern Slavery Act Transparency Statement|Sitemap|About US| Contact US: help@patsnap.com