Numerical controller controlling five-axis processing machine
A numerical control device and processing device technology, applied in the direction of digital control, program control, computer control, etc., can solve the problems of rough processing and time-consuming processing, achieve the effect of smooth processing shape, eliminate shaking, and shorten processing time
- Summary
- Abstract
- Description
- Claims
- Application Information
AI Technical Summary
Problems solved by technology
Method used
Image
Examples
Embodiment Construction
[0030] Image 6 It is a schematic functional block diagram of an embodiment of a numerical control device for controlling a 5-axis machining device according to the present invention.
[0031] A block of an NC program as a machining program is analyzed in the command reading unit 1, and a predetermined thinning process is executed by the thinning unit 2 ( Figure 12 Processes representing flowcharts of algorithms represented in ). For the machine coordinate position of the linear axis and the rotational position of the rotary axis for which the predetermined thinning process has been performed, the interpolation unit 3 performs interpolation processing for obtaining the position of each axis in each interpolation cycle, so that the tool tip point is on the moving path. Move at the commanded relative speed. Then, the servo motors 4x, 4y, 4z, 4b(a), and 4c of the axes are controlled based on the interpolated data in this way.
[0032] Figure 7A as well as Figure 7B is des...
PUM
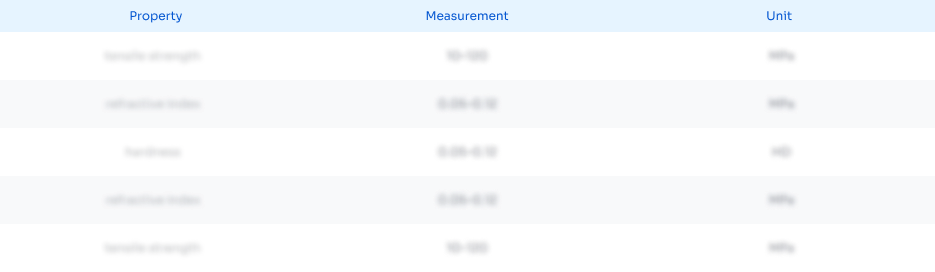
Abstract
Description
Claims
Application Information

- R&D
- Intellectual Property
- Life Sciences
- Materials
- Tech Scout
- Unparalleled Data Quality
- Higher Quality Content
- 60% Fewer Hallucinations
Browse by: Latest US Patents, China's latest patents, Technical Efficacy Thesaurus, Application Domain, Technology Topic, Popular Technical Reports.
© 2025 PatSnap. All rights reserved.Legal|Privacy policy|Modern Slavery Act Transparency Statement|Sitemap|About US| Contact US: help@patsnap.com