High expansion foam fire-extinguishing system
A foam fire-extinguishing and high-expansion technology, used in fire rescue and other directions, can solve the problems of not being able to catch up, not being able to form side by side at the same time, poor foaming rate, etc., so as to reduce the reduction of foaming rate and prevent the reduction of foaming rate. , the compact effect of the foamer
- Summary
- Abstract
- Description
- Claims
- Application Information
AI Technical Summary
Problems solved by technology
Method used
Image
Examples
no. 1 example
[0086] use Figure 1 ~ Figure 3 A first embodiment of the present invention will be described.
[0087]In a room (chamber) as a fire monitoring area, a foamer B of high-expansion foam fire extinguishing equipment is installed. The foaming rate of this foamer B is set to 500, for example.
[0088] The foamer B is cylindrical, for example, has a foamer body 1 with a square cross-section, its transverse length L is, for example, 900 mm, and its longitudinal length (height) H is, for example, 640 mm. The net 2 for foaming is provided in the front-end|tip 1a side of this foamer main body 1. As shown in FIG. On the side of the rear end 1b of the foamer main body 1, at a predetermined distance from the foaming net 2, for example, 90 cm, a spray nozzle 3 is installed inside. The spray nozzle 3 sprays the foam solution W in a conically expanding spray pattern WP toward the foaming net 2 .
[0089] The inside of the foamer main body 1 is divided by an intermediate net 4 . The inter...
no. 2 example
[0100] use Figure 4 The second embodiment of the present invention is described, with Figure 1 ~ Figure 3 The same reference numerals have the same names and functions. In addition, the structure of the foam generator (foam generator of this embodiment) of this embodiment is different from that of the first embodiment, and the system structure other than that is substantially the same.
[0101] The difference between this embodiment and the first embodiment is the arrangement position of the intermediate net 4 . That is, the arrangement position P1 is a limit position where the liquid droplets of the foam solution W sprayed from the spray nozzle 3 can maintain a flow velocity that can pass through the meshes of the intermediate net 4 .
[0102] As mentioned above, in this embodiment, the area from the arrival position P0 where the outer periphery of the spray pattern hits the inner wall of the foamer main body to the extreme position P1 where the liquid droplets can pass t...
no. 3 example
[0105] use Figure 5 , Figure 6 The third embodiment of the present invention is described, with Figure 1 ~ Figure 3 The same reference numerals have the same names and functions. In addition, the structure of the foam generator (foam generator of this embodiment) of this embodiment is different from that of the first embodiment, and the system structure other than that is substantially the same.
[0106] This embodiment differs from the first embodiment in that a plurality of spray nozzles 3 are provided. The number of the spray nozzles 3 is, for example, four, and these spray nozzles 3 are arranged side by side, and their front ends are located on the same vertical plane.
[0107] The present invention is not limited to the above-mentioned embodiments, and for example, the intermediate net 4 may be installed obliquely at a predetermined angle instead of vertically. The inclination angle can be appropriately selected within a range of, for example, 1 to 30 degrees.
[...
PUM
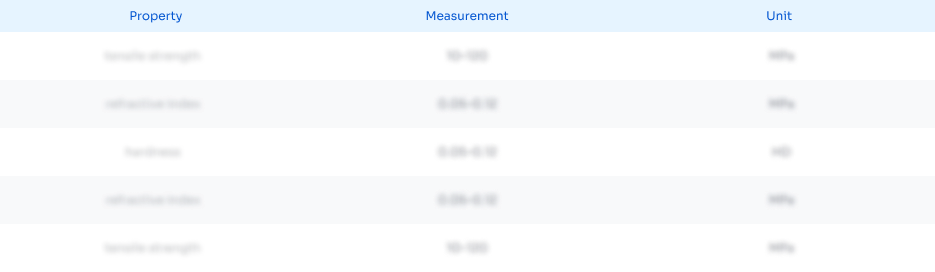
Abstract
Description
Claims
Application Information

- R&D
- Intellectual Property
- Life Sciences
- Materials
- Tech Scout
- Unparalleled Data Quality
- Higher Quality Content
- 60% Fewer Hallucinations
Browse by: Latest US Patents, China's latest patents, Technical Efficacy Thesaurus, Application Domain, Technology Topic, Popular Technical Reports.
© 2025 PatSnap. All rights reserved.Legal|Privacy policy|Modern Slavery Act Transparency Statement|Sitemap|About US| Contact US: help@patsnap.com