High chamber temperature process and chamber design for photo-resist stripping and post-metal etch passivation
A technology of process gas and chamber body, applied in the direction of discharge tubes, electrical components, circuits, etc., can solve the problems of increasing the overall complexity of chamber design and manufacturing costs.
- Summary
- Abstract
- Description
- Claims
- Application Information
AI Technical Summary
Problems solved by technology
Method used
Image
Examples
Embodiment Construction
[0016] A strip chamber is described for increasing the stripping rate of photoresist on a substrate disposed within the chamber. Certain embodiments may include, inter alia, a gas distribution assembly having a very small surface area exposed to the gas, and including a plurality of gas channels formed therein, wherein the gas fans out as the gas passes through the channels. The stripping chamber may also include an inner chamber body that forms a dome-shaped cavity to further fan the gas and thereby provide a uniform distribution of gas flow over the surface of the substrate. The "dome-shaped" cavity preferably has a width or diameter that decreases away from the substrate, ie the cavity may be conical, hemispherical, concave or other shape.
[0017] In stripping or ashing processes using a gas, the gas can have a high flow rate and high pressure, creating a high gas velocity at the opening of the downstream stripping chamber. In some applications, this velocity can be as hi...
PUM
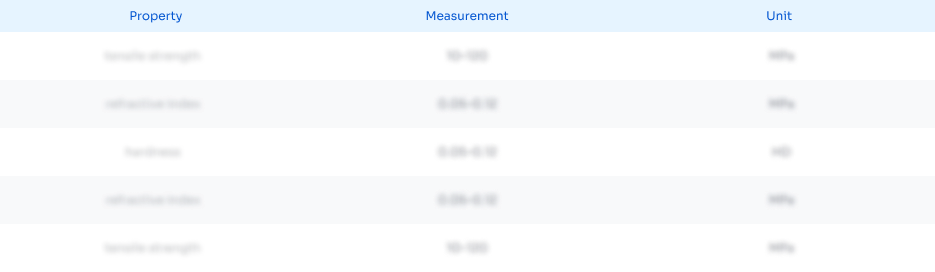
Abstract
Description
Claims
Application Information

- Generate Ideas
- Intellectual Property
- Life Sciences
- Materials
- Tech Scout
- Unparalleled Data Quality
- Higher Quality Content
- 60% Fewer Hallucinations
Browse by: Latest US Patents, China's latest patents, Technical Efficacy Thesaurus, Application Domain, Technology Topic, Popular Technical Reports.
© 2025 PatSnap. All rights reserved.Legal|Privacy policy|Modern Slavery Act Transparency Statement|Sitemap|About US| Contact US: help@patsnap.com