Tappet assembly for a high-pressure pump and high-pressure pump comprising at least one tappet assembly
A high-pressure pump and push rod technology, which is applied to components with teeth, pumps, multi-cylinder pumps, etc., can solve problems such as increasing manufacturing costs, and achieve the effect of avoiding edge support and a simple method.
- Summary
- Abstract
- Description
- Claims
- Application Information
AI Technical Summary
Problems solved by technology
Method used
Image
Examples
Embodiment Construction
[0014] exist Figures 1 to 8 A high-pressure pump for a fuel injection system for an internal combustion engine is shown in . The high-pressure pump has a multi-part housing 10 in which a rotationally driven drive shaft 12 is arranged. The drive shaft 12 is mounted rotatably in the housing 10 via two bearing points spaced apart from one another in the direction of the axis of rotation 13 of the drive shaft 12 . These bearing points can be provided in different parts 14 , 16 of the housing 10 .
[0015] In the region between these two bearing points, the drive shaft 12 has at least one cam 26 or eccentric, wherein the cam 26 can also be designed as a multi-way cam. The high-pressure pump has at least one or more pump units 32 each arranged in a housing part 18 and each having a pump piston 34 which is indirectly driven via the cam 26 of the drive shaft 12 to drive A reciprocating linear movement is performed in at least approximately radial direction of the axis of rotation ...
PUM
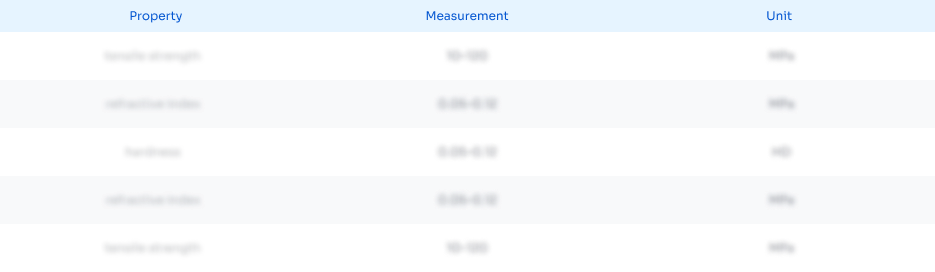
Abstract
Description
Claims
Application Information

- R&D
- Intellectual Property
- Life Sciences
- Materials
- Tech Scout
- Unparalleled Data Quality
- Higher Quality Content
- 60% Fewer Hallucinations
Browse by: Latest US Patents, China's latest patents, Technical Efficacy Thesaurus, Application Domain, Technology Topic, Popular Technical Reports.
© 2025 PatSnap. All rights reserved.Legal|Privacy policy|Modern Slavery Act Transparency Statement|Sitemap|About US| Contact US: help@patsnap.com