Rock deforming and cracking three-dimensional dynamic testing system based on fiber strain sensing
A fiber optic strain and three-dimensional dynamic technology, applied in the direction of applying stable tension/pressure to test the strength of materials, measuring devices, using optical devices, etc., can solve the problem of poor anti-interference effect, can only be pasted on the rock surface, cannot be completed, etc. question
- Summary
- Abstract
- Description
- Claims
- Application Information
AI Technical Summary
Problems solved by technology
Method used
Image
Examples
Embodiment 1
[0020] Example 1: figure 1 Among them, the test piece 1 is cylindrical, and its outer side and end surface are respectively provided with a number of micro-holes 8, and the cylinder inner wall, outer side and end surface of the test piece 1 are also provided with a number of long micro-grooves 9, fiber grating sensor 2 are respectively laid in the micro-hole 8 and the long micro-groove 9, and evenly arranged on the inner surface of the cylinder of the test piece 1; the fiber grating sensor 2 arranged on the outer side and end surface of the test piece 1 is sealed and sealed with high-strength glue Fixed to ensure effective coupling between the fiber grating sensor 2 and the surface of the rock specimen 1. The fiber grating sensor 2 is connected to the optical switch 4 through the optical fiber 3, and the optical switch 4 is connected to the fiber demodulation instrument 5. The fiber grating sensor 2 in the microhole 8 is mainly used to test the strain changes in the internal hor...
Embodiment 2
[0021] Example 2: Such as figure 2 As shown, the test piece 1 is cylindrical, the outer side and end surface of the test piece 1 are provided with a number of micro-holes 8, and the inner wall, the outer side and the end surface of the test piece 1 are provided with a number of long micro-grooves 9, long period The grating 6 is laid on the inner surface of the cylinder and in the micro-holes 8 and long micro-grooves 9 on the inner wall, outer side and end surface of the cylinder. One end of the long-period grating 6 is a broadband light source, and the other end is connected to a spectrum analyzer 7 for Analyze the transmission spectrum of the long period grating. The long-period grating 6 in the microhole 8 is mainly used to test the strain changes in the internal horizontal (ie X and Y directions) direction; the long-period grating 6 in the long microgrooves 9 on the inner and outer surfaces of the specimen 1 is mainly used To test the strain change in the vertical (Z direct...
Embodiment 3
[0022] Example 3: Specimen 1 is square, and the outer surface of specimen 1 is provided with a number of micro-holes 8 and a number of long micro-grooves 9, long-period grating 6 is laid in the micro-holes 8 and the long micro-grooves 9, long-period grating One end of 6 is a broadband light source, and the other end is connected to a spectrum analyzer 7 for analyzing the transmission spectrum of the long period grating.
[0023] In the present invention image 3 Indicates the direction of the pressure exerted by the three-axis press on the specimen. The specimen is placed in a sealed pressure chamber, and the upper and lower ends of the specimen are compressed by σ z , The inside of the test piece is filled with high-pressure oil and sealed, causing outward pressure σ rl , After the outer surface of the test piece is sealed by external high-pressure oil, an inward pressure σ is generated ro .
[0024] Figure 4 It is a process of applying a fiber grating sensor in a long micro-groov...
PUM
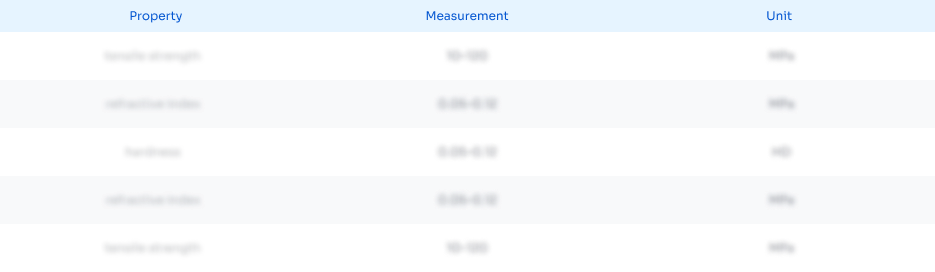
Abstract
Description
Claims
Application Information

- R&D Engineer
- R&D Manager
- IP Professional
- Industry Leading Data Capabilities
- Powerful AI technology
- Patent DNA Extraction
Browse by: Latest US Patents, China's latest patents, Technical Efficacy Thesaurus, Application Domain, Technology Topic, Popular Technical Reports.
© 2024 PatSnap. All rights reserved.Legal|Privacy policy|Modern Slavery Act Transparency Statement|Sitemap|About US| Contact US: help@patsnap.com