Decoupling micromechanical gyroscope
A micro-mechanical gyroscope and decoupling technology, which is applied in the direction of speed measurement by gyro effect, gyroscope/steering sensing equipment, and measuring devices, etc. It can solve the problems of small capacitance change, small comb-tooth structure detection capacitance, and difficult measurement. , to achieve the effect of increasing capacitance variation, making full use of space, and saving manufacturing costs
- Summary
- Abstract
- Description
- Claims
- Application Information
AI Technical Summary
Problems solved by technology
Method used
Image
Examples
Embodiment Construction
[0025] Hereinafter, the advantages of the present invention will be described through a preferred embodiment of the present invention.
[0026] figure 1 It is a schematic diagram of the silicon structure of the micromechanical gyroscope of the preferred embodiment of the present invention. The silicon structure 12 includes:
[0027] A movable symmetrical grid-shaped central mass 2, which has a grid arranged along the y-axis direction, wherein the y-axis is the detection direction, and the x-axis perpendicular to it is the driving direction; the upper and lower sides of the central mass pass through The inner detection support beam 13 is connected to the drive comb structure 3, and its left and right sides are connected to the detection comb structure 4 through the inner drive support beam 14;
[0028] The driving comb structure 3 is symmetrically distributed on the left and right sides of the central mass, and is connected to the anchor points 9 located at the upper and lowe...
PUM
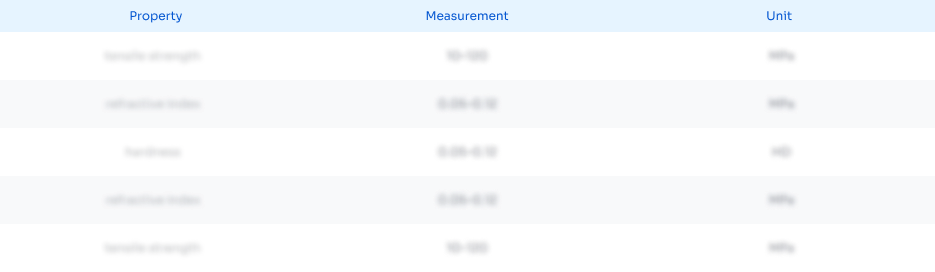
Abstract
Description
Claims
Application Information

- R&D
- Intellectual Property
- Life Sciences
- Materials
- Tech Scout
- Unparalleled Data Quality
- Higher Quality Content
- 60% Fewer Hallucinations
Browse by: Latest US Patents, China's latest patents, Technical Efficacy Thesaurus, Application Domain, Technology Topic, Popular Technical Reports.
© 2025 PatSnap. All rights reserved.Legal|Privacy policy|Modern Slavery Act Transparency Statement|Sitemap|About US| Contact US: help@patsnap.com