Fan drive system
A driving system and fan technology, which is applied in fluid pressure actuated system components, engine components, engine cooling, etc., can solve the problems of increasing the number of hydraulic pumps, a large amount of installation space, and high cost, so as to reduce the pump capacity, The effect of preventing waste and stabilizing operation
- Summary
- Abstract
- Description
- Claims
- Application Information
AI Technical Summary
Problems solved by technology
Method used
Image
Examples
Embodiment 1
[0056] use figure 1 and figure 2 , the hydraulic circuit including the fan drive system according to the first embodiment of the present invention will be described. figure 1 A simplified hydraulic circuit diagram is shown in, figure 2 A detailed hydraulic circuit diagram is shown in . First, use figure 1 , briefly explaining the hydraulic circuit of the fan driving system according to the first embodiment of the present invention, and then using figure 2 , the hydraulic circuit including the fan drive system according to the first embodiment of the present invention will be described. Also, in figure 1 and figure 2 Common part numbers are described using the same part number.
[0057] like figure 1 As shown, the discharge flow rate from the load pressure sensitive variable displacement pump 1 driven by an engine not shown is discharged to the discharge oil passage 51 which is the first discharge oil passage. The discharge oil passage 51 branches off from an ...
Embodiment 2
[0122] use image 3 and Figure 4 , will describe a hydraulic circuit diagram of a fan drive system according to a second embodiment of the present invention. In the second embodiment, in addition to the hydraulic circuit configuration of the first embodiment, a circuit configuration in which a steering drive circuit is added is formed. In addition, as the load pressure in the hydraulic control oil passage 78 as the first hydraulic control oil passage led to the shuttle valve 29, each of the steering drive unit 30, the lift cylinders 13A, 13B, and the dump cylinders 20A, 20B is used. The highest load pressure among load pressures. In this structure, Example 2 is formed as a structure different from that of Example 1, but other structures are formed as the same structures as those in Example 1.
[0123] Therefore, among the configurations of the second embodiment, the same components as those of the first embodiment are assigned the same reference numerals as those used in t...
Embodiment 3
[0158] Figure 5 , Image 6Each of the drawings shows a hydraulic circuit diagram of a fan drive system including a third embodiment of the present invention. In Embodiment 3 and Embodiment 1 or Embodiment 2, the circuit structure in Embodiment 3 is different from that in Embodiment 1 and Embodiment 2 regarding the circuit structure for guiding the load pressure to the hydraulic control oil passage 80 . other structures in Figure 5 Formed as the loop structure as the embodiment 1 figure 2 The same loop structure, in Image 6 Formed as the loop structure as the embodiment 2 Figure 4 same loop structure.
[0159] Therefore, in the non-configured priority valve 3 Figure 5 In FIG. 2 , for the same structure as in Embodiment 1, description thereof is omitted by using the same part numbers as those used in Embodiment 1. FIG. In addition, when using the priority valve 3 Image 6 In , for the same structure as in Embodiment 2, description thereof is omitted by using the sa...
PUM
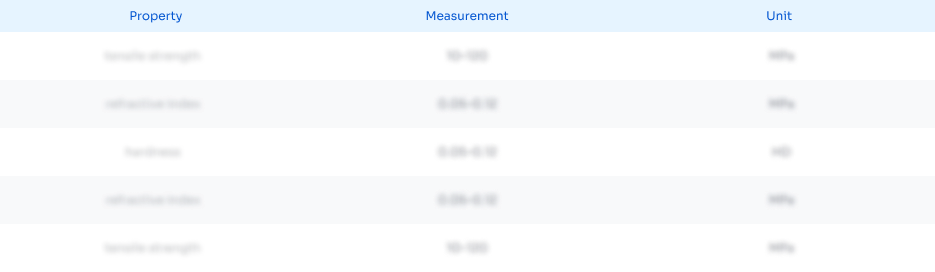
Abstract
Description
Claims
Application Information

- R&D
- Intellectual Property
- Life Sciences
- Materials
- Tech Scout
- Unparalleled Data Quality
- Higher Quality Content
- 60% Fewer Hallucinations
Browse by: Latest US Patents, China's latest patents, Technical Efficacy Thesaurus, Application Domain, Technology Topic, Popular Technical Reports.
© 2025 PatSnap. All rights reserved.Legal|Privacy policy|Modern Slavery Act Transparency Statement|Sitemap|About US| Contact US: help@patsnap.com