Rapid thermal firing ir conveyor furnace having high intensity heating section
A heat treatment furnace and conveyor belt technology, applied in the field of metallization and sintering, can solve the problems affecting the heat distribution curve, lamp vibration, fatigue failure output, etc., and achieve the effects of increasing production volume, increasing production capacity, and increasing speed.
- Summary
- Abstract
- Description
- Claims
- Application Information
AI Technical Summary
Problems solved by technology
Method used
Image
Examples
Embodiment Construction
[0064] The following detailed description sets forth the present invention by way of example, rather than limiting the scope, equivalents or principles of the present invention. This description clearly enables one of ordinary skill in the art to understand and use the invention, and describes several embodiments, modifications, variations, substitutions and uses of the invention, including what is presently believed to be the best mode of carrying out the invention.
[0065] In this regard, the invention has been illustrated in multiple figures and is of sufficient complexity that the many components, interrelationships, and subcombinations thereof cannot be fully illustrated in only a single patent type figure. For purposes of clarity and conciseness, the various figures are shown schematically or with the omission of components that are not essential to describing the specific structures, aspects or principles of the disclosed inventions. For example, the various electrical...
PUM
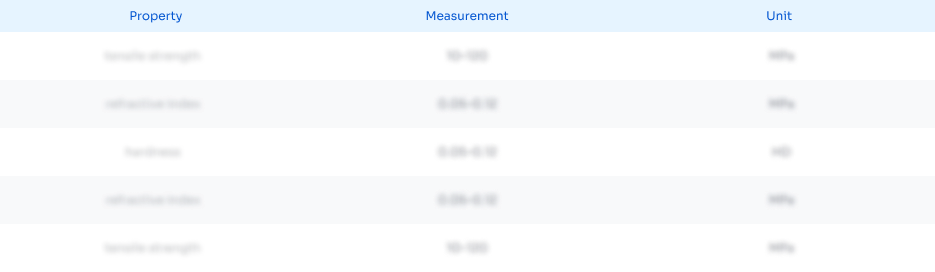
Abstract
Description
Claims
Application Information

- Generate Ideas
- Intellectual Property
- Life Sciences
- Materials
- Tech Scout
- Unparalleled Data Quality
- Higher Quality Content
- 60% Fewer Hallucinations
Browse by: Latest US Patents, China's latest patents, Technical Efficacy Thesaurus, Application Domain, Technology Topic, Popular Technical Reports.
© 2025 PatSnap. All rights reserved.Legal|Privacy policy|Modern Slavery Act Transparency Statement|Sitemap|About US| Contact US: help@patsnap.com