Spring plate open window waste-fetching technological process
A process method and shrapnel technology, applied in metal processing and other directions, can solve the problems of product scrap, product adhesion, contamination, etc., and achieve the effect of saving labor costs and improving efficiency
- Summary
- Abstract
- Description
- Claims
- Application Information
AI Technical Summary
Problems solved by technology
Method used
Image
Examples
Embodiment Construction
[0023] like figure 1 The window-opening waste removal process method of the shown shrapnel
[0024] Use the shrapnel, scraper and suction collection system to suck up the waste pieces of the inner frame.
[0025] The shrapnel arranged in the direction of 45 degrees on the outer frame die-cut product material plane, the oblique scraper is set on the front of the outer frame die-cut product material plane surface and the shrapnel, and the tip of the scraper is close to the outer frame die-cut product material plane surface. There is an air suction port of the air suction collection system above the plane surface of the outer frame die-cut product material between the scraper and the scraper. During the plane travel of the outer frame die-cut product material:
[0026] The first step is to bounce off one side of the inner frame of the product by using the shrapnel 2 that is 45 degrees from the plane of the die-cut product material 1 of the outer frame.
[0027] The second step...
PUM
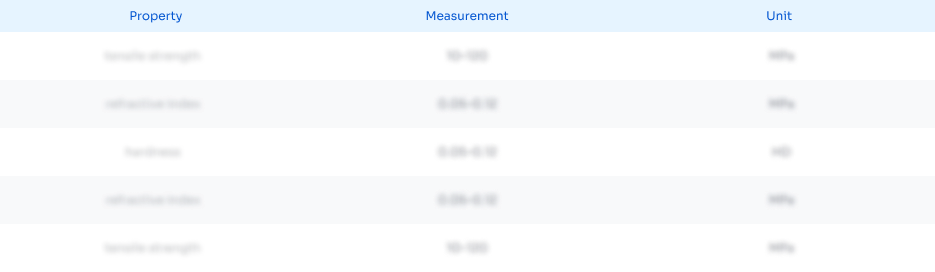
Abstract
Description
Claims
Application Information

- R&D
- Intellectual Property
- Life Sciences
- Materials
- Tech Scout
- Unparalleled Data Quality
- Higher Quality Content
- 60% Fewer Hallucinations
Browse by: Latest US Patents, China's latest patents, Technical Efficacy Thesaurus, Application Domain, Technology Topic, Popular Technical Reports.
© 2025 PatSnap. All rights reserved.Legal|Privacy policy|Modern Slavery Act Transparency Statement|Sitemap|About US| Contact US: help@patsnap.com