Improved inner expansion type tube extension device
An internal expansion type and pipe technology, applied in the direction of workpiece clamping device, manufacturing tools, etc., can solve the problems of increased pipe consumption, high manufacturing cost, and increased processing procedures, so as to improve work efficiency, reduce subsequent processing procedures, and reliable processing Effect
- Summary
- Abstract
- Description
- Claims
- Application Information
AI Technical Summary
Problems solved by technology
Method used
Image
Examples
Embodiment Construction
[0011] See figure 1 , figure 2 , image 3 and Figure 4 , the present invention includes a sleeve, an inner tie rod 1, an expansion block 2 and an elastic ferrule 3, the sleeve includes a connection part 4 and an expansion joint part 5, the inner tie rod 1 is set inside the sleeve, and the sleeve expansion joint part 5 A sliding groove is formed along the circumference, the expansion block 2 is embedded in the sliding groove, and the elastic ferrule 3 is sleeved on the periphery of the expansion joint part 5 of the sleeve. The inner tie rod 1 has an oblique cone structure at the expansion joint part 5 of the sleeve; the inner tie rod 1 and the sleeve are connected and fixed by the lock nut 7; there are five sliding grooves; five expansion blocks 2 are arranged; The outer diameter of the connecting part 4 of the sleeve is the same as that of the finned tube to be processed; the connection between the connecting part 4 of the sleeve and the joint part 5 is a step surface, an...
PUM
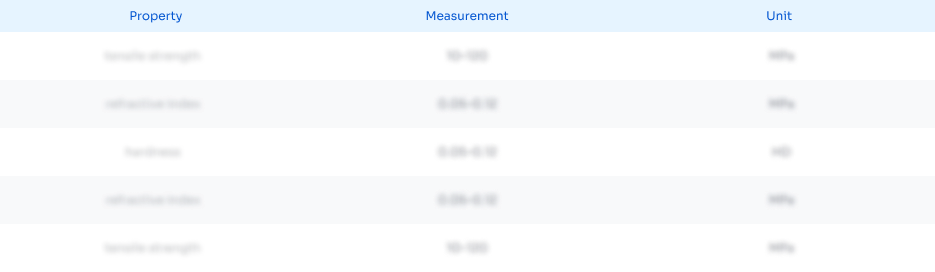
Abstract
Description
Claims
Application Information

- R&D
- Intellectual Property
- Life Sciences
- Materials
- Tech Scout
- Unparalleled Data Quality
- Higher Quality Content
- 60% Fewer Hallucinations
Browse by: Latest US Patents, China's latest patents, Technical Efficacy Thesaurus, Application Domain, Technology Topic, Popular Technical Reports.
© 2025 PatSnap. All rights reserved.Legal|Privacy policy|Modern Slavery Act Transparency Statement|Sitemap|About US| Contact US: help@patsnap.com