Preparation technique of 5-methoxy-2-tetralone
A preparation process, technology of dimethoxynaphthalene, applied in the field of preparation of tetralone compounds, can solve the problems of low selectivity and difficult purification of 5-methoxy-2-tetralone
- Summary
- Abstract
- Description
- Claims
- Application Information
AI Technical Summary
Problems solved by technology
Method used
Image
Examples
Embodiment 1
[0031] In a 1000mL four-necked bottle, add 1,6-dimethoxynaphthalene (1,6-OCH 3 ) 42g, absolute ethanol 289g, liquid ammonia 8.4g, stir until fully dissolved. Press 35g of sodium into filaments and add to the reaction solution in batches, adding 5g of Na each time, after 5g of Na disappears, continue to add 5g of Na. Control the rate of adding Na and the rate of heating so that the reduction temperature is at 25-35°C. From the beginning of sodium addition to the end of reduction, it takes about 48 hours.
[0032] Water was added dropwise to the reducing solution for dilution, and the mixture of ethanol and water was distilled off. Add water to the residual liquid of the kettle, stir and dilute, and separate the oil layer. The oil layer was mixed with dilute hydrochloric acid, stirred, refluxed for hydrolysis, and the oil layer was separated to obtain 5-methoxy-2-tetralone with a yield of 81%.
[0033] As a result of gas chromatography analysis, 5-methoxy-2-tetralone was 46....
Embodiment 2
[0035] In a 1000mL four-necked bottle, add 1,6-dimethoxynaphthalene (1,6-OCH 3 ) 42g, absolute ethanol 340g, liquid ammonia 14.5g, stir until fully dissolved. Press 35g of sodium into filaments and add to the reaction solution in batches, adding 5g of Na each time, after 5g of Na disappears, continue to add 5g of Na. Control the rate of adding Na and the rate of heating so that the reduction temperature is between 15°C and 25°C. It takes about 40 hours from the beginning of sodium addition to the end of reduction.
[0036] Water was added dropwise to the reducing solution for dilution, and the mixture of ethanol and water was distilled off. Add water to the residual liquid of the kettle, stir and dilute, and separate the oil layer. The oil layer was mixed with dilute hydrochloric acid, stirred, refluxed and hydrolyzed, and the oil layer was separated to obtain 5-methoxy-2-tetralone with a yield of 82%.
[0037] As a result of gas chromatography analysis, 5-methoxy-2-tetral...
Embodiment 3
[0039] In a 1000mL four-necked bottle, add 1,6-dimethoxynaphthalene (1,6-OCH 3 ) 42g, absolute ethanol 370g, liquid ammonia 2.5g, stir until fully dissolved. Press 42g of sodium into filaments and add to the reaction liquid in batches, adding 5g of Na each time, after 5g of Na disappears, continue to add 5g of Na. Control the rate of adding Na and the rate of heating so that the reduction temperature is at 25-35°C. From the beginning of sodium addition to the end of reduction, it takes about 38 hours.
[0040] Water was added dropwise to the reducing solution for dilution, and the mixture of ethanol and water was distilled off. Add water to the residual liquid of the kettle, stir and dilute, and separate the oil layer. The oil layer was mixed with dilute hydrochloric acid, stirred, refluxed for hydrolysis, and the oil layer was separated to obtain 5-methoxy-2-tetralone with a yield of 79%.
[0041] As a result of gas chromatography analysis, 5-methoxy-2-tetralone was 44.9%...
PUM
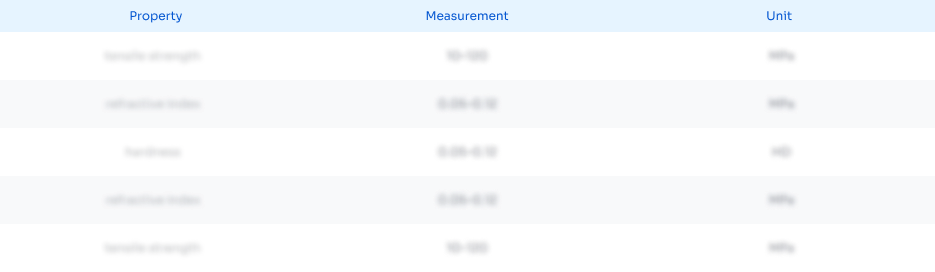
Abstract
Description
Claims
Application Information

- Generate Ideas
- Intellectual Property
- Life Sciences
- Materials
- Tech Scout
- Unparalleled Data Quality
- Higher Quality Content
- 60% Fewer Hallucinations
Browse by: Latest US Patents, China's latest patents, Technical Efficacy Thesaurus, Application Domain, Technology Topic, Popular Technical Reports.
© 2025 PatSnap. All rights reserved.Legal|Privacy policy|Modern Slavery Act Transparency Statement|Sitemap|About US| Contact US: help@patsnap.com