Equipment for etching uniwafer of silicon wafer back face
A backside, silicon wafer technology, used in electrical components, semiconductor/solid-state device manufacturing, circuits, etc., can solve the problems of dielectric film etching and affect the quality of the dielectric film on the back of the product, and achieve the effect of reducing over-etching and ensuring quality.
- Summary
- Abstract
- Description
- Claims
- Application Information
AI Technical Summary
Problems solved by technology
Method used
Image
Examples
Embodiment Construction
[0013] Such as figure 1 , 2 As shown, the silicon wafer back monolithic etching equipment of the present invention includes a controller, and also includes an endpoint detection device (EPD), which includes a light source emitter, a reflected light receiving sensor and a signal processing system, and the light source emits The device emits light to the back of the silicon wafer, and the reflected light receiving sensor is used to receive the reflected light emitted by different dielectric films on the back of the silicon wafer for the emitted light (see figure 1 ), and convert the information of the reflected light into a current signal and transmit it to the signal processing system, the signal processing system determines the end point detection result according to the reflected light information, and transmits the detection signal of the end point detection result to the controller (see figure 2 ), the controller controls the etching process of the chemical solution to st...
PUM
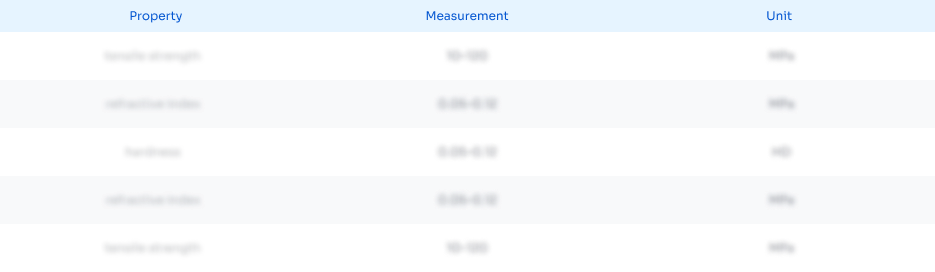
Abstract
Description
Claims
Application Information

- R&D
- Intellectual Property
- Life Sciences
- Materials
- Tech Scout
- Unparalleled Data Quality
- Higher Quality Content
- 60% Fewer Hallucinations
Browse by: Latest US Patents, China's latest patents, Technical Efficacy Thesaurus, Application Domain, Technology Topic, Popular Technical Reports.
© 2025 PatSnap. All rights reserved.Legal|Privacy policy|Modern Slavery Act Transparency Statement|Sitemap|About US| Contact US: help@patsnap.com