Full-mold casting technique of resin-bonded sand
A casting process and solid mold casting technology, which is applied in the field of resin sand solid mold casting process, can solve the problems of pollution and the easy filling and dissatisfaction of castings.
- Summary
- Abstract
- Description
- Claims
- Application Information
AI Technical Summary
Problems solved by technology
Method used
Image
Examples
Embodiment Construction
[0015] Specific embodiments of the present invention will be described in detail below with reference to the accompanying drawings.
[0016] A kind of preferred resin sand solid mold casting process provided by the present invention comprises the following steps: manufacture pattern 4, manufacture pattern 4 with foam material; Coating and drying, coat and hang coating on pattern 4 surface, and dry; Moulding, dry The pattern 4 is placed in the sand box 10, the sprue is placed, the sand box 10 is filled with resin sand 5 for molding, and the riser 6 is set on the pattern 4; , after cooling, open the box to shake out the sand, and clean the casting; wherein, during the pouring process, the sand box 10 maintains a vacuum state.
[0017] According to the resin sand casting process provided by the present invention, since the sand box 10 maintains a vacuum state during the pouring process, a large amount of waste gas and smoke generated by the foam pattern 4 can be sucked away by th...
PUM
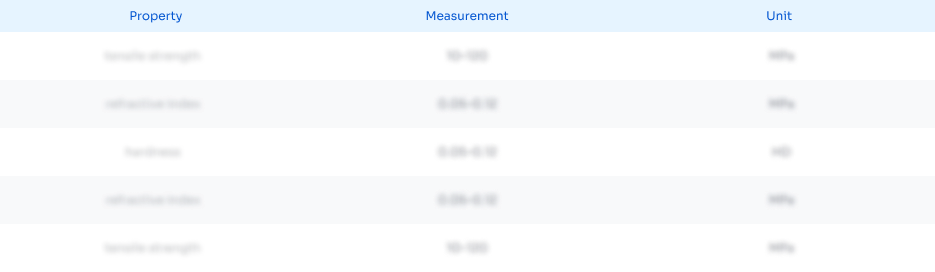
Abstract
Description
Claims
Application Information

- R&D
- Intellectual Property
- Life Sciences
- Materials
- Tech Scout
- Unparalleled Data Quality
- Higher Quality Content
- 60% Fewer Hallucinations
Browse by: Latest US Patents, China's latest patents, Technical Efficacy Thesaurus, Application Domain, Technology Topic, Popular Technical Reports.
© 2025 PatSnap. All rights reserved.Legal|Privacy policy|Modern Slavery Act Transparency Statement|Sitemap|About US| Contact US: help@patsnap.com