Shell circumferential-seam welding method using plasma welding
A technology of plasma welding and container cylinder, which is applied to the welding of the circular seam of the container cylinder, and in the field of plasma welding and welding of the circular seam of the container cylinder, which can solve the problems of incomplete penetration, increased welding thickness, arc column offset weld bead, etc. Achieve good welding quality
- Summary
- Abstract
- Description
- Claims
- Application Information
AI Technical Summary
Problems solved by technology
Method used
Image
Examples
Embodiment 1
[0034] Embodiment 1. The inner diameter of the cylinder is 2000 mm, the plate thickness is 14 mm, and the material is zirconium (Zr-60702).
Embodiment 2
[0035] Embodiment 2, the inner diameter of the cylinder is 2000 mm, the plate thickness is 14 mm, and the material is stainless steel (304).
[0036] Because the plate thickness exceeds the thickness of one-time penetration, therefore, according to the new "Y" type groove type of the present invention, a groove is provided on the butt joint, and the wide side of the groove is arranged on the inner wall of the cylinder (that is, the new "Y" shape) . Strictly control the difference in length and diagonal length during the barrel blanking and beveling process, and strictly control the roundness of the barrel after it is rolled into the barrel, and strictly control the alignment gap and misalignment when the two barrels are aligned quantity. If the roundness is too large, it will affect the welding quality.
[0037] For materials with this plate thickness, conduct welding evaluation according to the regulations, determine the welding process parameters of plasma welding, as show...
PUM
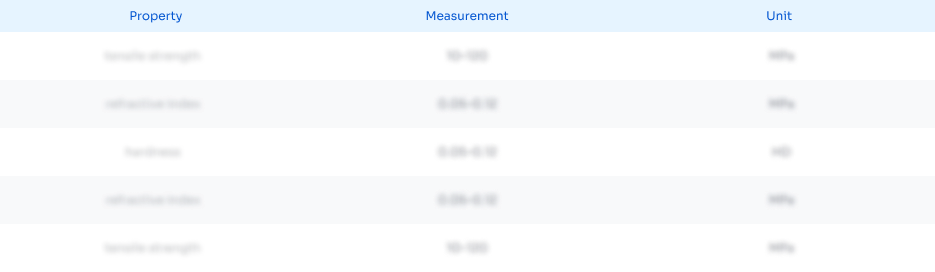
Abstract
Description
Claims
Application Information

- R&D Engineer
- R&D Manager
- IP Professional
- Industry Leading Data Capabilities
- Powerful AI technology
- Patent DNA Extraction
Browse by: Latest US Patents, China's latest patents, Technical Efficacy Thesaurus, Application Domain, Technology Topic, Popular Technical Reports.
© 2024 PatSnap. All rights reserved.Legal|Privacy policy|Modern Slavery Act Transparency Statement|Sitemap|About US| Contact US: help@patsnap.com