Low-temperature plasticizing type PVC plastic colloidal sols and method of producing the same
A plastisol, PVC resin technology, applied in coatings, polyurea/polyurethane coatings, etc., can solve the problems of high drying room temperature, high plasticizing temperature, unfavorable energy saving and emission reduction in automobile production plants, etc., and reduce the drying room temperature. , the effect of reducing the plasticizing temperature
- Summary
- Abstract
- Description
- Claims
- Application Information
AI Technical Summary
Problems solved by technology
Method used
Examples
Embodiment 1
[0014] Preparation of closed polyurethane prepolymer: Add 50 parts of diluent to the three-neck reactor, heat up to 75°C while stirring, then add 100 parts of polyisocyanate, and then slowly add 250 parts of polyether polyol to react for 3 hours Afterwards, slowly add 10 parts of dimethylpyrazoles and continue to react for 2 hours;
[0015] Preparation of low-temperature plasticized PVC plastisol: Add 10 parts of closed polyurethane prepolymer and 5 parts of low-molecular polyamide resin to 200 parts of plasticizer and disperse evenly, then add the rest of the components and disperse evenly , and then put the uniformly dispersed material into a biaxial stirrer and stir for 30 minutes, and vacuumize while stirring until the vacuum degree is 0.09MPa, then place it at room temperature for 24 hours to mature the PVC plastisol, and then filter;
[0016] Among them, the remaining components include 100 parts of PVC resin paste, 5 parts of heat stabilizer, 150 parts of nano-active ca...
Embodiment 2
[0018] Preparation of closed polyurethane prepolymer: Add 300 parts of diluent to the three-neck reactor, heat up to 77°C while stirring, then add 250 parts of isophorone diisocyanate, and then slowly add 500 parts of polyether polyol After reacting for 3.5 hours, slowly add 110 parts of dimethylpyrazole and 1 part of catalyst to continue the reaction for 2.5 hours;
[0019] Preparation of low-temperature plasticized PVC plastisol: Add 55 parts of closed polyurethane prepolymer and 22 parts of low-molecular polyamide resin to 350 parts of plasticizer and disperse evenly, then add the rest of the components and disperse evenly , and then put the uniformly dispersed material into a biaxial stirrer and stir for 30 minutes, and vacuumize while stirring until the vacuum degree is 0.09MPa, then place it at room temperature for 24 hours to mature the PVC plastisol, and then filter;
[0020] Among them, the remaining components include 300 parts of PVC resin paste, 150 parts of chlori...
Embodiment 3
[0022] Preparation of closed polyurethane prepolymer: Add 500 parts of diluent to the three-neck reactor, heat up to 80°C while stirring, then add 400 parts of isophorone diisocyanate (IPDI) derivatives, and then slowly add After 800 parts of polyether polyols were reacted for 4 hours, slowly add 200 parts of dimethylpyrazole and 2 parts of catalysts to continue the reaction for 3 hours;
[0023] Preparation of low-temperature plasticized PVC plastisol: Add 100 parts of closed polyurethane prepolymer and 40 parts of low-molecular-weight polyamide resin to 500 parts of plasticizer and disperse evenly, then add the rest of the components and disperse evenly , and then put the uniformly dispersed material into a biaxial stirrer and stir for 30 minutes, and vacuumize while stirring until the vacuum degree is 0.09MPa, then place it at room temperature for 24 hours to mature the PVC plastisol, and then filter;
[0024] Among them, the remaining components include 500 parts of PVC re...
PUM
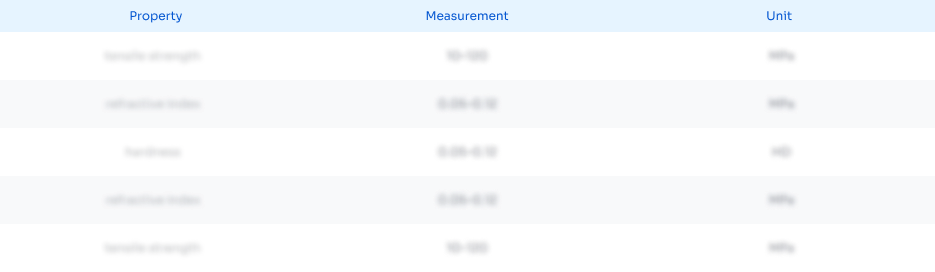
Abstract
Description
Claims
Application Information

- R&D Engineer
- R&D Manager
- IP Professional
- Industry Leading Data Capabilities
- Powerful AI technology
- Patent DNA Extraction
Browse by: Latest US Patents, China's latest patents, Technical Efficacy Thesaurus, Application Domain, Technology Topic, Popular Technical Reports.
© 2024 PatSnap. All rights reserved.Legal|Privacy policy|Modern Slavery Act Transparency Statement|Sitemap|About US| Contact US: help@patsnap.com