Beneficiation method and apparatus for fine granule attractive mineral
A beneficiation method and fine-grained technology, applied in chemical instruments and methods, magnetic separation, wet separation, etc., can solve the problem of low recovery rate of fine-grained magnetic materials, unfavorable separation of non-magnetic materials, and enrichment ratio of centrifugal concentrators. Low-level problems, to achieve the effect of strengthening the efficiency of sorting and recycling, reducing the amount of magnetic blocks, and highly targeted
- Summary
- Abstract
- Description
- Claims
- Application Information
AI Technical Summary
Problems solved by technology
Method used
Image
Examples
Embodiment Construction
[0024] The beneficiation method of fine-grained magnetic minerals of the present invention is to set the gradient and rotating speed of the sorting drum with the components of the mineral material. Under the force of the magnetic field, it is adsorbed on the sorting drum and rotates with it, and the non-magnetic minerals and weakly magnetic minerals are washed with rinsing water to separate the non-magnetic minerals and weak magnetic minerals, so that they move to the lower end of the sorting drum to the tailings discharge hopper and discharged. Under the action of relative motion between the sorting drum and the spiral magnetic system, the minerals move spirally to the high end of the sorting drum, and after leaving the magnetic field, they are discharged to the concentrate discharge hopper through the spiral unloading plate and discharged.
[0025] The beneficiation device used to realize the beneficiation method of the fine-grained magnetic mineral of the present invention i...
PUM
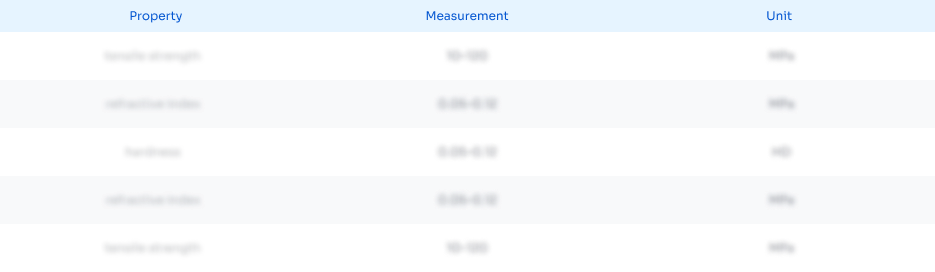
Abstract
Description
Claims
Application Information

- R&D Engineer
- R&D Manager
- IP Professional
- Industry Leading Data Capabilities
- Powerful AI technology
- Patent DNA Extraction
Browse by: Latest US Patents, China's latest patents, Technical Efficacy Thesaurus, Application Domain, Technology Topic, Popular Technical Reports.
© 2024 PatSnap. All rights reserved.Legal|Privacy policy|Modern Slavery Act Transparency Statement|Sitemap|About US| Contact US: help@patsnap.com