Flame-retardant ASA material and preparation method thereof
A technology based on weight percentage and styrene, which is applied in the field of flame-retardant ASA materials and its preparation, can solve the problems of material brittleness, poor flame-retardant performance, and reduced toughness, so as to overcome the sharp decrease in toughness, improve flame retardancy, and maintain toughness Effect
- Summary
- Abstract
- Description
- Claims
- Application Information
AI Technical Summary
Problems solved by technology
Method used
Examples
Embodiment 1
[0036] The ternary graft copolymer (ASA) weight ratio of its acrylonitrile, styrene, acrylate composition of resin is: 82%; Toughener weight ratio is: 2%; Tetrabromobisphenol A weight ratio is: 12% ; Antimony trioxide (Sb 2 o 3 ) weight ratio is: 3%; UV absorber (5411) weight ratio is: 0.3%; antioxidant (1010) weight ratio is: 0.2%; antioxidant (168) weight ratio is: 0.2%; lubricant ( EBS) weight ratio: 0.3%. Mix for 4 minutes in a high-speed mixer;
[0037] The uniformly mixed components are placed in a twin-screw extruder, melted, mixed, extruded and granulated;
[0038] The temperature of the first zone of the twin-screw extruder: 180~190℃, the temperature of the second zone: 190~200℃, the temperature of the third zone: 200~210℃, the temperature of the fourth zone: 210~220℃, the temperature of the fifth zone: 200~210℃ , Six-zone temperature: 190-200°C, residence time 1-2 minutes, host speed: 300-350rpm.
Embodiment 2
[0040]The ternary graft copolymer (ASA) weight ratio of its acrylonitrile, styrene, acrylate composition of resin is: 80%; Toughener weight ratio is: 3.3%; Tetrabromobisphenol A weight ratio is: 13% ; Antimony trioxide (Sb 2 o 3 ) weight ratio: 3%; UV absorber (5411) weight ratio: 0.3%; antioxidant (1010) weight ratio: 0.05%; antioxidant (168) weight ratio: 0.05%; lubricant ( EBS) weight ratio: 0.3%. Mix for 4 minutes in a high-speed mixer;
[0041] Put the homogeneously mixed components in a twin-screw extruder, melt, mix, extrude and granulate;
[0042] The temperature of the first zone of the twin-screw extruder: 180~190℃, the temperature of the second zone: 190~200℃, the temperature of the third zone: 200~210℃, the temperature of the fourth zone: 210~220℃, the temperature of the fifth zone: 200~210℃ , Six-zone temperature: 190-200°C, residence time 1-2 minutes, host speed: 300-350rpm.
Embodiment 3
[0044] The ternary graft copolymer (ASA) weight ratio of its acrylonitrile, styrene, acrylate composition of resin is: 76%; Toughener weight ratio is: 3.2%; Tetrabromobisphenol A weight ratio is: 15% ; Antimony trioxide (Sb 2 o 3 ) weight ratio is: 4%; UV absorber (5411) weight ratio is: 0.4%; antioxidant (1010) weight ratio is: 0.5%; antioxidant (168) weight ratio is: 0.5%; lubricant ( EBS) weight ratio: 0.4%. Mix for 4 minutes in a high-speed mixer;
[0045] The uniformly mixed raw materials are placed in a twin-screw extruder, melted, mixed, extruded and granulated;
[0046] The temperature of the first zone of the twin-screw extruder: 180~190℃, the temperature of the second zone: 190~200℃, the temperature of the third zone: 200~210℃, the temperature of the fourth zone: 210~220℃, the temperature of the fifth zone: 200~210℃ , Six-zone temperature: 190-200°C, residence time 1-2 minutes, host speed: 300-350rpm.
PUM
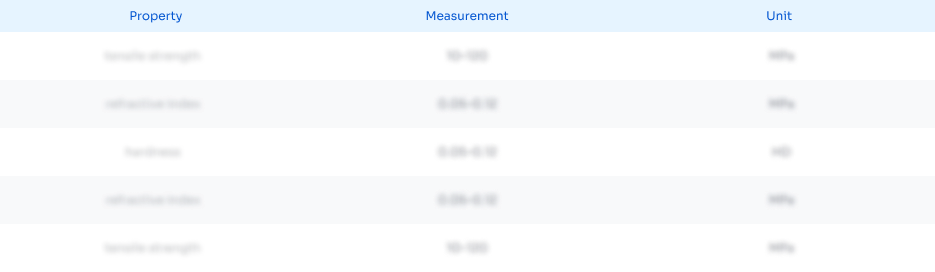
Abstract
Description
Claims
Application Information

- R&D
- Intellectual Property
- Life Sciences
- Materials
- Tech Scout
- Unparalleled Data Quality
- Higher Quality Content
- 60% Fewer Hallucinations
Browse by: Latest US Patents, China's latest patents, Technical Efficacy Thesaurus, Application Domain, Technology Topic, Popular Technical Reports.
© 2025 PatSnap. All rights reserved.Legal|Privacy policy|Modern Slavery Act Transparency Statement|Sitemap|About US| Contact US: help@patsnap.com