Method for manufacturing magnetoresistance element and apparatus for manufacturing magnetoresistance element
A magnetoresistance effect element and manufacturing method technology, applied in the manufacture/processing of electromagnetic devices, resistors controlled by magnetic fields, etc., can solve the problems of lower MR ratio and difficulty in achieving low RA and high MR ratio at the same time
- Summary
- Abstract
- Description
- Claims
- Application Information
AI Technical Summary
Benefits of technology
Problems solved by technology
Method used
Image
Examples
Embodiment Construction
[0081] refer to figure 1 , figure 2 as well as image 3 , to illustrate the first embodiment of the present invention. figure 1 It is a diagram showing an example of the thin film structure of the magnetoresistance effect element having the MgO insulator layer manufactured in the first example.
[0082] figure 1 In, SiO is formed on the surface 2 On a Si (silicon) substrate 12 made of (silicon dioxide), a lower electrode layer 9 (thickness 10 nm) made of Ta (tantalum) and an antiferromagnetic layer 8 (film thickness 10 nm) made of PtMn (platinum manganese) are laminated. 15nm thick), CoFe (cobalt iron) layer 6 (film thickness 2.5nm), Ru (ruthenium) layer 5 (film thickness 0.85nm), first ferromagnetic layer 2 (film thickness 3nm) formed by CoFeB (cobalt iron boron) ), an insulator layer 4 (thickness 1.0nm) made of MgO (magnesium oxide), a second ferromagnetic layer 3 (thickness 3nm) made of CoFeB (cobalt iron boron), and an upper electrode made of Ta (tantalum) layer 10 ...
PUM
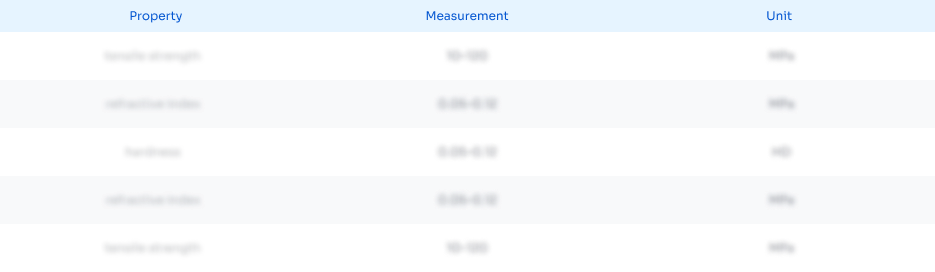
Abstract
Description
Claims
Application Information

- Generate Ideas
- Intellectual Property
- Life Sciences
- Materials
- Tech Scout
- Unparalleled Data Quality
- Higher Quality Content
- 60% Fewer Hallucinations
Browse by: Latest US Patents, China's latest patents, Technical Efficacy Thesaurus, Application Domain, Technology Topic, Popular Technical Reports.
© 2025 PatSnap. All rights reserved.Legal|Privacy policy|Modern Slavery Act Transparency Statement|Sitemap|About US| Contact US: help@patsnap.com