Anti sling liquid for welding
An anti-splash and concentration technology, applied in the field of chemical coatings, can solve the problems of poor paint adhesion, affect health, low efficiency, etc., and achieve the effect of low cost
- Summary
- Abstract
- Description
- Claims
- Application Information
AI Technical Summary
Problems solved by technology
Method used
Examples
Embodiment 1
[0009] Example 1: According to the weight ratio, water: calcium oxide: ink with a concentration of 1% is mixed at a ratio of 100.0:20:0.5. The above-mentioned preparation materials are placed in a container and stirred evenly, and then the prepared solution is filtered. The generally used filter screen is 80 to 100 mesh, and then spray or paint it in the range of about 100 mm in the area to be welded, and then it can be welded. The calcium oxide in the present invention is dissolved in water to form calcium hydroxide, and then naturally dried to form calcium carbonate. The high temperature generated during welding can easily dry the coating liquid and form a layer of isolation film, which can effectively prevent high-temperature splash and adhesion on the surface of the workpiece. The solder balls splashed on the surface of the workpiece can fall off by themselves or fall off with one touch. After the workpiece is soldered, when removing the anti-splash liquid residue, use a dry r...
Embodiment 2
[0010] Example 2: According to the weight ratio, water: calcium oxide: ink with a concentration of 1% = 100: 25: 0.8. The preparation method and use method of this example are the same as that of Example 1. The preparation materials are placed in a container and stirred evenly, and then sprayed or coated on the area to be welded within about 100 mm, and then welded after a little dry. The use effect of Example 2 is basically the same as that of Example 1.
Embodiment 3
[0011] Example 3: According to the weight ratio, water: calcium oxide: ink with a concentration of 1%=100.0:30:1 was mixed. The preparation method and use method of this example are the same as those of example 1. The use effect of Example 3 and the use effect of Example 1 are also basically the same. The invention can also be used to prevent blocking of the welding torch, and can be used by dip coating on the head of the welding torch.
PUM
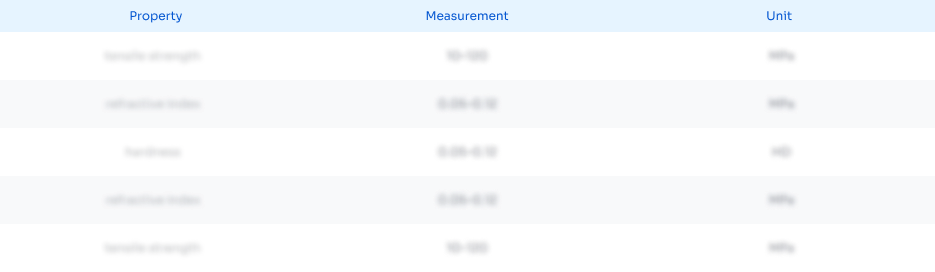
Abstract
Description
Claims
Application Information

- R&D
- Intellectual Property
- Life Sciences
- Materials
- Tech Scout
- Unparalleled Data Quality
- Higher Quality Content
- 60% Fewer Hallucinations
Browse by: Latest US Patents, China's latest patents, Technical Efficacy Thesaurus, Application Domain, Technology Topic, Popular Technical Reports.
© 2025 PatSnap. All rights reserved.Legal|Privacy policy|Modern Slavery Act Transparency Statement|Sitemap|About US| Contact US: help@patsnap.com