Multi-foot robot pressure-spring limitation type elastic driving joint module
A multi-legged robot, elastic drive technology, applied in the direction of manipulators, manufacturing tools, joints, etc., can solve the problems that the appearance is too large, can not be widely used in bionic multi-legged robots, etc., to achieve energy efficiency, compact structure, reliable self-locking Effect
- Summary
- Abstract
- Description
- Claims
- Application Information
AI Technical Summary
Problems solved by technology
Method used
Image
Examples
Embodiment Construction
[0022] The present invention is described in more detail below in conjunction with accompanying drawing example:
[0023] to combine Figure 1 to Figure 5 , each modular transmission structure is driven by a servo motor through a reducer. The transmission mechanism adopts a worm gear mechanism, which makes the input and output axes orthogonal, and has self-locking and adjustable characteristics. The worm gear output block passes the movement of the worm gear through Four compression springs are transferred to the joint output. The module mainly includes: fixing screw 1, motor rear end cover 2, connecting flange 3, four fixing screws 4, four connecting copper pillars 5, servo motor 6, thrust bearing 7, motor and box fixing screw 8, Fixed pin 9, potentiometer 10, pin 11, worm gear output block 12, potentiometer support frame 13, fixing screw 14, transmission joint block 15, adjustable fastening screw 16, worm screw 17, worm gear 18, fixing screw 19, support bearing I20, steel ...
PUM
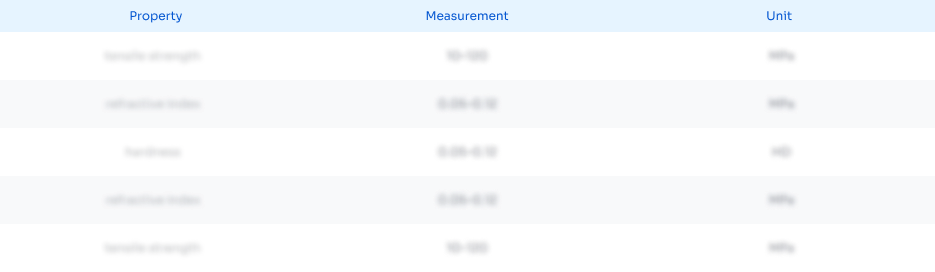
Abstract
Description
Claims
Application Information

- Generate Ideas
- Intellectual Property
- Life Sciences
- Materials
- Tech Scout
- Unparalleled Data Quality
- Higher Quality Content
- 60% Fewer Hallucinations
Browse by: Latest US Patents, China's latest patents, Technical Efficacy Thesaurus, Application Domain, Technology Topic, Popular Technical Reports.
© 2025 PatSnap. All rights reserved.Legal|Privacy policy|Modern Slavery Act Transparency Statement|Sitemap|About US| Contact US: help@patsnap.com