Method for recycling sludge of sewage plant to produce cement
A sewage plant and sludge technology, applied in cement production, chemical instruments and methods, sludge treatment, etc., can solve the problems of long treatment cycle, secondary pollution, high operating cost, improve burnability, save land, The effect of saving land resources
- Summary
- Abstract
- Description
- Claims
- Application Information
AI Technical Summary
Problems solved by technology
Method used
Image
Examples
specific Embodiment approach
[0021] (1) Sludge iron removal: use magnetism to remove metallic iron in sludge.
[0022] (2) Sterilization and deodorization of sludge: Quicklime is used as a sterilizing and deodorizing agent and added to the sludge at a ratio of 1% to 5%.
[0023] (3) Dehydration and drying treatment of sludge: use natural drying in the air, filter press dehydration and drying, centrifugal dehydration and vacuum dehydration and drying techniques to dehydrate and dry the sludge to make the sludge moisture less than 20%.
[0024] (4) Determine the amount of sludge blending: when the heavy metal content in the sludge meets the standards in the table below, determine that the upper limit of the amount of sludge blending is 20%; when the heavy metal content in the sludge exceeds the limit standard in the table below, determine that the sludge The upper limit of the blending amount is 10% (the above-mentioned sludge blending amount is based on the dried sludge).
[0025] Cd Cu Pb ...
PUM
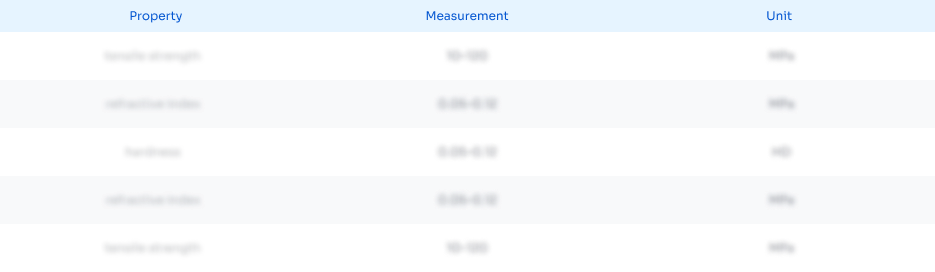
Abstract
Description
Claims
Application Information

- Generate Ideas
- Intellectual Property
- Life Sciences
- Materials
- Tech Scout
- Unparalleled Data Quality
- Higher Quality Content
- 60% Fewer Hallucinations
Browse by: Latest US Patents, China's latest patents, Technical Efficacy Thesaurus, Application Domain, Technology Topic, Popular Technical Reports.
© 2025 PatSnap. All rights reserved.Legal|Privacy policy|Modern Slavery Act Transparency Statement|Sitemap|About US| Contact US: help@patsnap.com