Novel process for directly melting fiber reinforced thermoplastic composite material
A composite material and fiber reinforced technology, applied in the new field of fiber reinforced thermoplastic composite material molding, can solve the problem of high production cost, achieve the effects of low production cost, reduced storage of ingredients, and easy reuse
- Summary
- Abstract
- Description
- Claims
- Application Information
AI Technical Summary
Problems solved by technology
Method used
Examples
Embodiment Construction
[0010] Below in conjunction with specific embodiment the present invention is described in further detail:
[0011] Taking the production of 1000kg thermoplastic composite material as an example, the proportion of raw material components is: polypropylene resin 60%, glass fiber 30%, silane coupling agent particles 2%, bismaimide 0.8%, ultraviolet absorber 0.1%, Antioxidant 1%, filler 8%; fiber-reinforced thermoplastic composite material direct melt impregnation and molding process combined process method, thermoplastic resin and ingredients are directly melted and then added to the mold for one-time molding. The specific process includes:
[0012] 1. Ingredients: First, according to the above ratio, dry 600kg of polypropylene resin, 300kg of glass fiber, 20kg of silane-type coupling agent particles, 8kg of bismaimide, 1kg of ultraviolet absorber, 10kg of antioxidant, and 80kg of filler according to a certain amount. Put into the reaction kettle after mixing in proportion;
[...
PUM
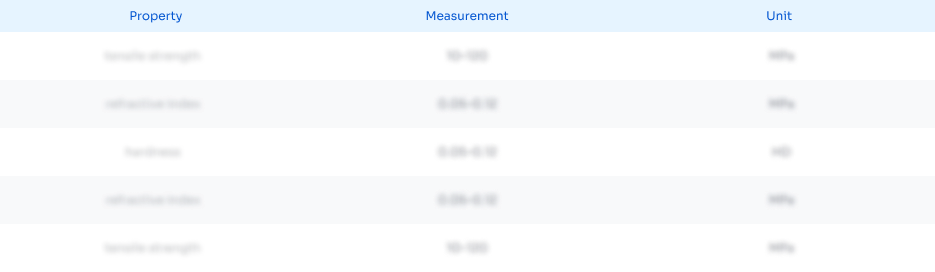
Abstract
Description
Claims
Application Information

- Generate Ideas
- Intellectual Property
- Life Sciences
- Materials
- Tech Scout
- Unparalleled Data Quality
- Higher Quality Content
- 60% Fewer Hallucinations
Browse by: Latest US Patents, China's latest patents, Technical Efficacy Thesaurus, Application Domain, Technology Topic, Popular Technical Reports.
© 2025 PatSnap. All rights reserved.Legal|Privacy policy|Modern Slavery Act Transparency Statement|Sitemap|About US| Contact US: help@patsnap.com