Method for processing fractured connecting rod for car engine
An automotive engine and processing method technology, applied in metal processing equipment, metal processing mechanical parts, manufacturing tools, etc., can solve the problems of high price, non-conformity, large cumulative error, etc., achieve low manufacturing accuracy requirements, and improve processing efficiency. , the effect of improving performance
- Summary
- Abstract
- Description
- Claims
- Application Information
AI Technical Summary
Problems solved by technology
Method used
Image
Examples
Embodiment Construction
[0019] Referring to Fig. 2, the connecting rod processed by the present invention consists of: small head hole 1, bushing 11, connecting rod body 2, fracture surface (bonding surface) 12, slip groove 13, big head hole 9, bolt 14, connecting rod cover 6 , upper and lower planes 8, bolt holes 15, small head oil holes 16, etc., are generally made of high carbon steel materials.
[0020] refer to image 3 , the main technological process of the present invention is: A, process connecting rod upper and lower plane; B, car small head hole; C, boring big and small head hole; D, drill bolt hole and tap; Bursting; G, assembly; H, fine boring and large and small head holes; I, fine grinding and large and small head holes; J, inspection. ...to the follow-up process.
[0021] With reference to Fig. 2,3,4,5,6,7,8, the concrete operation description of the present invention:
[0022] A. Machining the upper and lower planes of the connecting rod: use a double-end grinder to process the upp...
PUM
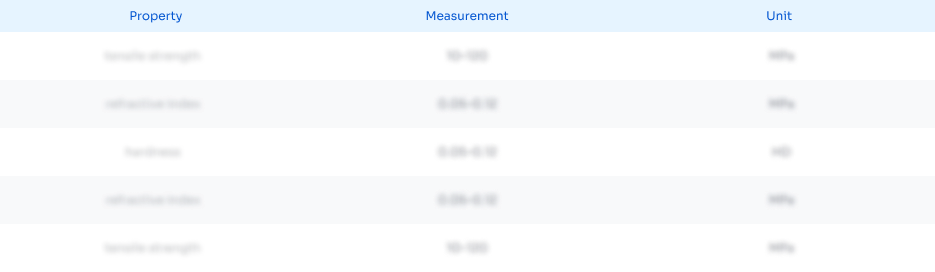
Abstract
Description
Claims
Application Information

- Generate Ideas
- Intellectual Property
- Life Sciences
- Materials
- Tech Scout
- Unparalleled Data Quality
- Higher Quality Content
- 60% Fewer Hallucinations
Browse by: Latest US Patents, China's latest patents, Technical Efficacy Thesaurus, Application Domain, Technology Topic, Popular Technical Reports.
© 2025 PatSnap. All rights reserved.Legal|Privacy policy|Modern Slavery Act Transparency Statement|Sitemap|About US| Contact US: help@patsnap.com