Laser amplifying measurement method for bending structure deformation
A technology of laser amplification and bending and torsion structure, which is applied in the direction of measuring devices, optical devices, instruments, etc., can solve the problems of insufficient accuracy, large measurement error, inconvenience, etc., and achieve the effect of avoiding insufficient accuracy
- Summary
- Abstract
- Description
- Claims
- Application Information
AI Technical Summary
Problems solved by technology
Method used
Image
Examples
Embodiment Construction
[0018] Such as figure 1 Shown:
[0019] First, according to the deformation characteristics of the specific bending and torsion structure or member to be measured, determine the measurement position of the bending and torsion member to be tested. The principle of general measurement point selection is to select the bending and torsion member to be tested to have the largest absolute rotation (rotation angle or torsion angle) as much as possible. parts. Then place the laser beam emitter together with the bracket on the point to be measured of the bending and torsion structure (object) to be measured, and rely on manual or mechanical aiming to align the beam with the pre-set light target reference position in the distance. When the load acts on the structure to be measured, the corresponding rotation (rotation angle or torsion angle) will occur at the measuring point. This turning or twisting angle will be magnified by the laser beam to a distant light target. By reading the ...
PUM
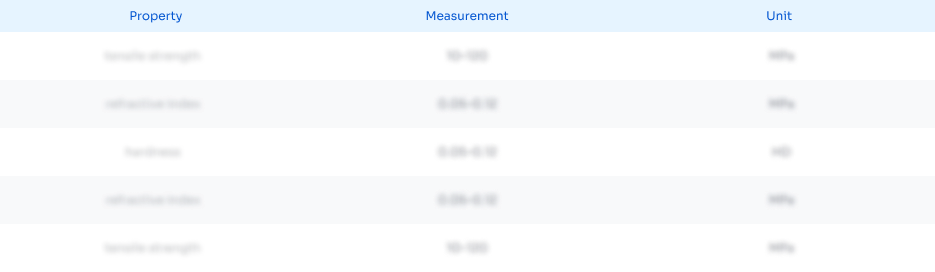
Abstract
Description
Claims
Application Information

- R&D
- Intellectual Property
- Life Sciences
- Materials
- Tech Scout
- Unparalleled Data Quality
- Higher Quality Content
- 60% Fewer Hallucinations
Browse by: Latest US Patents, China's latest patents, Technical Efficacy Thesaurus, Application Domain, Technology Topic, Popular Technical Reports.
© 2025 PatSnap. All rights reserved.Legal|Privacy policy|Modern Slavery Act Transparency Statement|Sitemap|About US| Contact US: help@patsnap.com