Hydrodesulphurization, olefin reduction method for gasoline
A technology for hydrogenation of gasoline and olefins, which is applied in the fields of hydrogenation treatment process, petroleum industry, and hydrocarbon oil treatment. It can solve the problems of low efficiency of accident treatment, small effective volume of catalyst loading, and reduction of sulfur content in gasoline products, so as to improve operation Flexibility and stability, reducing the coking problem of the catalytic bed, and reducing the hydrogen consumption of the device
- Summary
- Abstract
- Description
- Claims
- Application Information
AI Technical Summary
Problems solved by technology
Method used
Image
Examples
Embodiment 1~6
[0029] This test mainly investigates the hydrogenation effect of the hydrogenation process of the present invention and the prior art. Take gasoline desulfurization, olefin reduction, and octane recovery as examples. The properties of the raw oil used in this test are shown in Table-1. In this test, the hydrogenation reaction was carried out on a continuous test device. Examples 1-3 The properties of catalysts packed in reactor catalyst beds A, B, C and D are shown in Table-2. Examples 4-6 The properties of catalysts packed in reactor catalyst beds A, B, C and D are shown in Table-4. The raw material oil feed temperature is 150°C, see Table-3 and Table-5 for the examples.
[0030] Table-1 Main Properties of Raw Oil
[0031]
[0032] Table-2 Physicochemical properties of the catalyst bed catalyst in the reactors of Examples 1 to 3
[0033] Catalyst number
A1
B1
C1
D1
Catalytic active component
Ni [1]
Pt [1]
Mo, Co ...
PUM
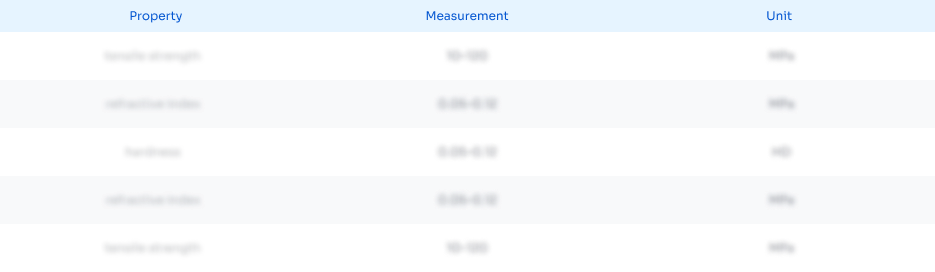
Abstract
Description
Claims
Application Information

- R&D
- Intellectual Property
- Life Sciences
- Materials
- Tech Scout
- Unparalleled Data Quality
- Higher Quality Content
- 60% Fewer Hallucinations
Browse by: Latest US Patents, China's latest patents, Technical Efficacy Thesaurus, Application Domain, Technology Topic, Popular Technical Reports.
© 2025 PatSnap. All rights reserved.Legal|Privacy policy|Modern Slavery Act Transparency Statement|Sitemap|About US| Contact US: help@patsnap.com