Method for casting and molding spiral rotor of compressor
A casting molding and compressor technology, which is applied to casting molding equipment, casting molds, casting mold components, etc., can solve problems such as damage to machine tools or cutting tools, waste of metal materials, and increased manufacturing costs, so as to simplify manufacturing procedures and reduce The effect of manufacturing cost and man-hour saving
- Summary
- Abstract
- Description
- Claims
- Application Information
AI Technical Summary
Problems solved by technology
Method used
Image
Examples
Embodiment Construction
[0018] Below in conjunction with accompanying drawing and specific embodiment the present invention is described in further detail:
[0019] The present invention is realized through the following steps:
[0020] A, prepare a first mold, and have an axially connected spiral part model in the first mold;
[0021] B. Prepare a sand mold, which is to pour mortar in the above-mentioned first mold, and after the mortar is solidified and shaped, the sand mold is formed after the model is demoulded, and a mold chamber with a spiral portion is formed in it;
[0022] C. Prepare a second mold, the second mold includes an upper sand box and a lower sand box, the sand mold is arranged in the lower sand box, and the upper sand box has a first pivot portion and a second pivot portion Mold cavity, positioning and combining the upper sand box and the lower sand box;
[0023] D. Casting, injecting the liquid casting material into the mold cavity and mold cavity, and after the casting materia...
PUM
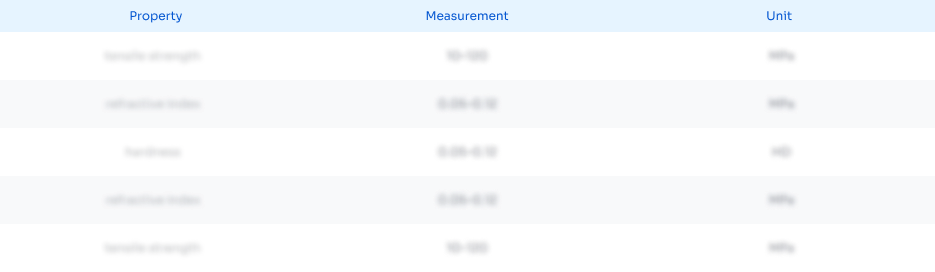
Abstract
Description
Claims
Application Information

- Generate Ideas
- Intellectual Property
- Life Sciences
- Materials
- Tech Scout
- Unparalleled Data Quality
- Higher Quality Content
- 60% Fewer Hallucinations
Browse by: Latest US Patents, China's latest patents, Technical Efficacy Thesaurus, Application Domain, Technology Topic, Popular Technical Reports.
© 2025 PatSnap. All rights reserved.Legal|Privacy policy|Modern Slavery Act Transparency Statement|Sitemap|About US| Contact US: help@patsnap.com