Machine tool main shaft axle journal shaft bushing friction performance test machine
A technology of machine tool spindles and tribology, applied in the field of tribology, can solve problems such as large errors, insufficient friction coefficient measurement methods, and complex structures
- Summary
- Abstract
- Description
- Claims
- Application Information
AI Technical Summary
Problems solved by technology
Method used
Image
Examples
Embodiment Construction
[0024] The technical scheme of the present invention is described in detail below in conjunction with accompanying drawing:
[0025] like figure 1 , figure 2 As shown, the present invention includes a driving part, a testing part, a loading part, and a measuring system;
[0026] The driving part includes frequency converter 1, speed regulating motor 2, coupling 3, support shaft 4, support 6, base 21; frequency converter 1 is connected with speed regulating motor 2, and the main shaft of speed regulating motor 2 is connected to The support shaft 4 is connected, the support shaft 4 is a stepped shaft, fixed on the support 6, and the support 6 is arranged on the base 21;
[0027] The test part includes a strain beam 14, an upper sample holder 13, an upper sample 12, a lower sample 11, and an oil ring 10; the strain beam 14 is vertically arranged on the upper end of the upper sample holder 13; The upper sample 12 is locked by screws, and the lower sample 11 is arranged under t...
PUM
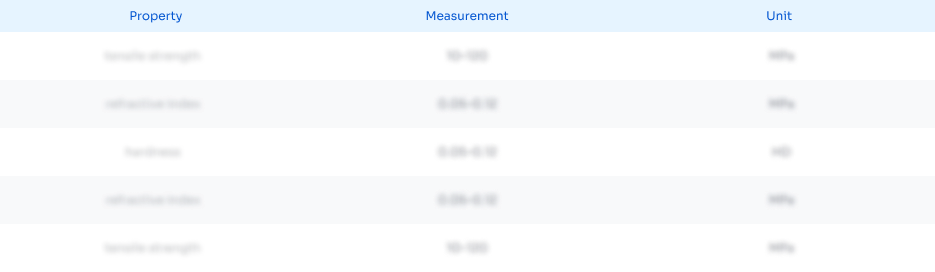
Abstract
Description
Claims
Application Information

- Generate Ideas
- Intellectual Property
- Life Sciences
- Materials
- Tech Scout
- Unparalleled Data Quality
- Higher Quality Content
- 60% Fewer Hallucinations
Browse by: Latest US Patents, China's latest patents, Technical Efficacy Thesaurus, Application Domain, Technology Topic, Popular Technical Reports.
© 2025 PatSnap. All rights reserved.Legal|Privacy policy|Modern Slavery Act Transparency Statement|Sitemap|About US| Contact US: help@patsnap.com