Burner brick for industrial kiln
A technology of burner bricks and kilns, which is applied in the direction of combustion chambers, combustion methods, and combustion equipment. It can solve the problems of easy expansion and deformation, high cost, and high temperature resistance, and achieves low expansion and deformation, low cost, and enhanced wear resistance. damaging effect
- Summary
- Abstract
- Description
- Claims
- Application Information
AI Technical Summary
Problems solved by technology
Method used
Image
Examples
Embodiment 1
[0017] Depend on figure 1 It can be seen that the burner brick for industrial kilns of the present invention includes a metal base 1 , a refractory inner liner 2 and a protective cover 3 . The metal base 1 is connected with the refractory inner container 2, and the center is connected. The metal base 1 has a burner gun inlet 5 for placing a burner gun, and a spark plug nozzle 6 for placing a spark plug, which can spray flames to the inside of the furnace. 3 sets of protective sleeves are used to protect the inner tank on the outside of the refractory inner tank 2, and the refractory fiber paper 4 is between the refractory inner tank 2 and the protective cover 3.
[0018] The metal base 1 contains the following components in parts by weight: 20 parts of chromium, 15 parts of aluminum, 20 parts of nickel, 5 parts of tungsten, and 40 parts of manganese. The above components are melted and casted at 1400-1500°C.
[0019] The refractory liner 2 contains the following components i...
Embodiment 2
[0023] The same as the burner brick in the embodiment, the difference is that the metal base 1 contains the following components in parts by weight: 15 parts of chromium, 15 parts of molybdenum, 15 parts of nickel, 3 parts of tungsten, and 30 parts of manganese. The refractory liner 2 contains the following components in parts by weight: 25 parts of mullite, 3 parts of silicon, 20 parts of alumina, 20 parts of corundum powder, and 5 parts of alumina cement.
Embodiment 3
[0025] The same as the burner brick in the embodiment, the difference is that the metal base 1 contains the following components in parts by weight: 30 parts of chromium, 30 parts of molybdenum, 30 parts of nickel, 7 parts of tungsten, and 45 parts of manganese. The refractory liner 2 contains the following components in parts by weight: 35 parts of mullite, 8 parts of silicon, 40 parts of alumina, 30 parts of corundum powder, and 10 parts of ordinary civil cement.
PUM
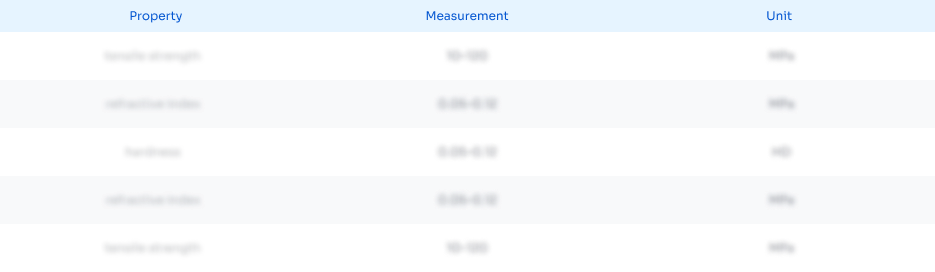
Abstract
Description
Claims
Application Information

- R&D Engineer
- R&D Manager
- IP Professional
- Industry Leading Data Capabilities
- Powerful AI technology
- Patent DNA Extraction
Browse by: Latest US Patents, China's latest patents, Technical Efficacy Thesaurus, Application Domain, Technology Topic, Popular Technical Reports.
© 2024 PatSnap. All rights reserved.Legal|Privacy policy|Modern Slavery Act Transparency Statement|Sitemap|About US| Contact US: help@patsnap.com