Heat-transferring die, manufacturing process and heat-transferring manufacturing process
A thermal transfer film and manufacturing process technology, applied in the field of thermal transfer film and its manufacturing process and thermal transfer manufacturing process, can solve the problem of small, applied in clothes, cloth bags, hats, pillows, mugs, porcelain Disks, tiles, watch cases, mouse pads, coasters, hanging calendars, medals, pennants, work cards, house numbers, mirror boxes, metal jugs, etc.
- Summary
- Abstract
- Description
- Claims
- Application Information
AI Technical Summary
Problems solved by technology
Method used
Image
Examples
Embodiment Construction
[0030] Such as figure 1 The schematic diagram of the embodiment of the structure and manufacturing process steps of the thermal transfer film 40 of the present invention is shown, including:
[0031] 1. The preparation step is to prepare a high-temperature-resistant film 1 with a release agent coating on its surface, so that it contains at least a high-temperature-resistant film 10 and a release agent coating 11;
[0032] 2. The printing step, using a printing device 2 to print a high temperature resistant ink layer 20 on the surface of the release agent coating 10; and
[0033] 3. Coating step, using a coating device 3 to coat a high-temperature-resistant heat-reactive hot-melt adhesive 30 on the high-temperature-resistant ink layer 20, thereby forming a high-temperature-resistant heat-reactive hot-melt adhesive on the high-temperature resistant ink layer 20 layer.
[0034] Through the above steps, the thermal transfer film 40 with a large area and unlimited length can be r...
PUM
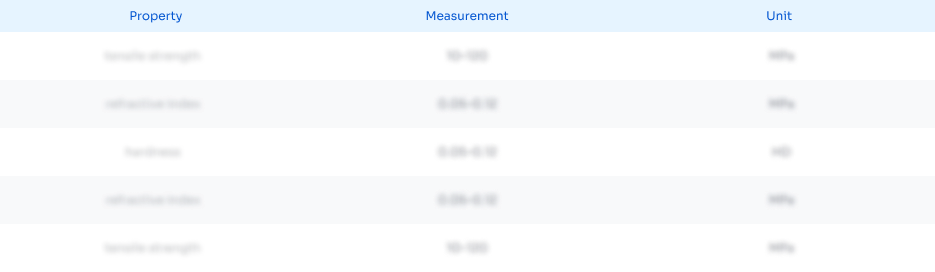
Abstract
Description
Claims
Application Information

- Generate Ideas
- Intellectual Property
- Life Sciences
- Materials
- Tech Scout
- Unparalleled Data Quality
- Higher Quality Content
- 60% Fewer Hallucinations
Browse by: Latest US Patents, China's latest patents, Technical Efficacy Thesaurus, Application Domain, Technology Topic, Popular Technical Reports.
© 2025 PatSnap. All rights reserved.Legal|Privacy policy|Modern Slavery Act Transparency Statement|Sitemap|About US| Contact US: help@patsnap.com