Method for preparing magnesium silicide and device
A technology of magnesium silicide and silicon powder, which is applied in the direction of metal silicide, etc., can solve problems such as device output and product quality limitations, obstacles to normal operation of mechanisms, and leakage of magnesium vapor, so as to reduce energy consumption and avoid product agglomeration and side effects. Response, the effect of saving dosage
- Summary
- Abstract
- Description
- Claims
- Application Information
AI Technical Summary
Problems solved by technology
Method used
Image
Examples
Embodiment 1
[0043] Silicon powder and magnesium powder are mixed according to the mass ratio of 1:1.7, and then poured into the preparation device of the present invention, and the temperature in the heating zone of the vertical cylindrical reactor is controlled at 550°C. Finally, the magnesium silicide product is obtained, such as figure 2 Shown is its XRD pattern, all XRD diffraction peaks in the pattern are consistent with the standard card 35-0773 of magnesium silicide, indicating that the product is magnesium silicide with high purity.
Embodiment 2
[0045] Silicon powder and magnesium powder are mixed according to the mass ratio of 1:1.5, and then poured into the preparation device of the present invention, and the temperature of the heating zone of the vertical cylindrical reactor is controlled at 650°C. Finally, a magnesium silicide product is obtained.
Embodiment 3
[0047] Silicon powder and magnesium powder are mixed according to the mass ratio of 1:2.3, and then poured into the preparation device of the present invention, and the temperature in the heating zone of the vertical cylindrical reactor is controlled at 500°C. Finally, a magnesium silicide product is obtained.
PUM
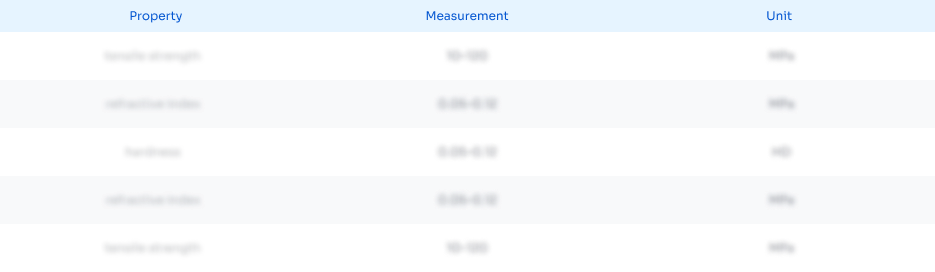
Abstract
Description
Claims
Application Information

- R&D Engineer
- R&D Manager
- IP Professional
- Industry Leading Data Capabilities
- Powerful AI technology
- Patent DNA Extraction
Browse by: Latest US Patents, China's latest patents, Technical Efficacy Thesaurus, Application Domain, Technology Topic, Popular Technical Reports.
© 2024 PatSnap. All rights reserved.Legal|Privacy policy|Modern Slavery Act Transparency Statement|Sitemap|About US| Contact US: help@patsnap.com