Magnetic bearing electromagnetic force sensing device based on optical fiber grating and on-line measurement system
A technology of optical fiber gratings and sensing devices, which is applied in the direction of using optical devices to transmit sensing components, measuring the change force of optical properties of materials when they are stressed, and can solve the problem of not being able to obtain the electromagnetic force distribution of a magnetic levitation rotor. Point distributed measurement, small size and other issues, to achieve the effect of easy embedding, high resolution and good stability
- Summary
- Abstract
- Description
- Claims
- Application Information
AI Technical Summary
Problems solved by technology
Method used
Image
Examples
Embodiment Construction
[0014] The specific embodiments of the present invention will be further described below in conjunction with the accompanying drawings.
[0015] The fiber grating-based magnetic bearing electromagnetic force sensing device reflects the change of the magnetic bearing electromagnetic force through the fiber grating wavelength shift, and realizes the non-contact online measurement of the magnetic force. The sensing device is composed of an L-shaped magnetically conductive elastic element 1 , a fiber grating 2 , a magnetic bearing stator 4 and a magnetic bearing rotor 5 . The installation method is that a thin groove 3 is engraved on the central axis of the L-shaped magnetically conductive elastic element 1, and the fiber grating 2 is packaged in the thin groove 3 by pasting. Axial grooves are engraved on the bottom of the magnetic poles of the magnetic bearing stator 4, and the front-end convex part of the L-shaped magnetically conductive elastic element 1 is glued into the magne...
PUM
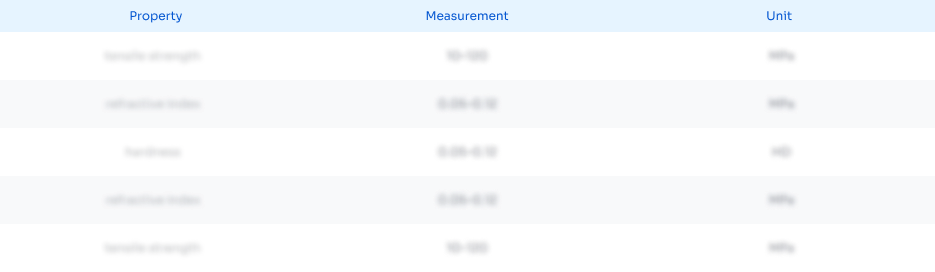
Abstract
Description
Claims
Application Information

- R&D
- Intellectual Property
- Life Sciences
- Materials
- Tech Scout
- Unparalleled Data Quality
- Higher Quality Content
- 60% Fewer Hallucinations
Browse by: Latest US Patents, China's latest patents, Technical Efficacy Thesaurus, Application Domain, Technology Topic, Popular Technical Reports.
© 2025 PatSnap. All rights reserved.Legal|Privacy policy|Modern Slavery Act Transparency Statement|Sitemap|About US| Contact US: help@patsnap.com