Energy-saving dimethyl ether production flow and apparatus thereof
A production device, a technology for dimethyl ether, which is applied in the field of new processes and devices, can solve the problems of wasting energy, reducing the thermodynamic efficiency of the separation process, and being unfavorable to economic benefits, so as to reduce the required energy, save equipment investment, and improve speed and efficiency. The effect of balancing conversion rates
- Summary
- Abstract
- Description
- Claims
- Application Information
AI Technical Summary
Problems solved by technology
Method used
Image
Examples
Embodiment 1
[0027] Embodiment 1: as figure 1 In the process shown, the bottom of the next-wall rectification column is heated by a reboiler, the operating pressure of the column is 0.9MPa, there are 11 theoretical plates in the top area 1 (including the condenser, the same below), and 32 theoretical plates in the left area 2 , there are 37 theoretical plates in zone 3, and 8 theoretical plates in zone 4 (including reboiler, the same below). The output flow rate of the reaction system is 5400kg / h, the pressure is 0.9MPa, the temperature is 135°C, the dimethyl ether content is 50% (mass fraction, the same below), the methanol content is 20%, and the water content is 30%. The middle part of distillation column area 2 enters. The raw material methanol is 2700kg / h, the temperature is 20°C, the methanol content is 99%, the water content is 1%, and it is added from the 31st theoretical plate (counted from the top of the tower, the same below). The dimethyl ether product is extracted from the t...
Embodiment 2
[0028] Embodiment 2: as figure 1 As shown in the flow process, the bottom of the rectifying column with the next wall is heated with a reboiler, the operating pressure of the column is 1MPa, and the number of theoretical plates in each area is the same as that of Example 1. The output flow rate of the reaction system is 5250kg / h, the pressure is 1MPa, the temperature is 140°C, the content of dimethyl ether is 45%, the content of methanol is 20%, and the content of water is 35%. The raw material methanol is 3000kg / h, the temperature is 30°C, the methanol content is 90%, and the water content is 10%, which is added from the 43rd theoretical plate. The dimethyl ether product is extracted from the top of the tower with a flow rate of 2362.5kg / h, of which the dimethyl ether content is 99.992%; the methanol vapor is extracted from the 15th theoretical plate and used as the feed of the reaction system for dehydration reaction with a flow rate of 3760.5kg / h, the methanol content is ...
Embodiment 3
[0029] Embodiment 3: as figure 1 As shown in the flow process, the bottom of the rectifying column is heated with a reboiler, the operating pressure of the column is 1MPa, and the number of theoretical plates in each area is the same as in Example 2. The output flow rate of the reaction system is 5250kg / h, the pressure is 1MPa, the temperature is 140°C, the content of dimethyl ether is 46%, the content of methanol is 18%, and the content of water is 36%. Raw material methanol 2850kg / h, temperature is 30 ℃, wherein methanol content is 80%, and water content is 20%, and its feeding position is the same as example 2. The dimethyl ether product is extracted from the top of the tower, the flow rate is 2415kg / h, and the dimethyl ether content is 99.992%; the methanol vapor is extracted from the rectifying column area 3 of the next wall, and the extraction position is the same as that of embodiment 2, and it is carried out as the feed of the reaction system Dehydration reaction, the...
PUM
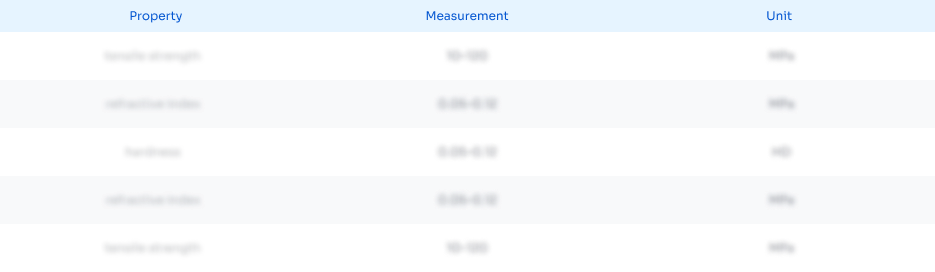
Abstract
Description
Claims
Application Information

- Generate Ideas
- Intellectual Property
- Life Sciences
- Materials
- Tech Scout
- Unparalleled Data Quality
- Higher Quality Content
- 60% Fewer Hallucinations
Browse by: Latest US Patents, China's latest patents, Technical Efficacy Thesaurus, Application Domain, Technology Topic, Popular Technical Reports.
© 2025 PatSnap. All rights reserved.Legal|Privacy policy|Modern Slavery Act Transparency Statement|Sitemap|About US| Contact US: help@patsnap.com