Novel regenerative environment-friendly rubber moulding board and manufacturing method thereof
An environmentally friendly rubber and manufacturing method technology, applied in the direction of formwork/formwork components, building structures, and on-site preparation of building components, can solve the problems of easy oxidation and rust, difficult waste cleaning, soft texture, etc., to achieve Good plasticity, good effect of promoting use value
- Summary
- Abstract
- Description
- Claims
- Application Information
AI Technical Summary
Problems solved by technology
Method used
Image
Examples
Embodiment Construction
[0017] as attached figure 1 And attached Figure 4 As shown, it is a schematic diagram of an embodiment of the present invention, which is to superimpose the outer layer composite material and the inner layer composite material produced according to the production process, and pressurize to form a new environmentally friendly recycled rubber template.
[0018] as attached figure 2 As shown, it is a schematic cross-sectional view of the outer layer composite material of the present invention, in which waste plastics, fly ash and other additives are mixed, stirred, heated, and pressurized to form an outer layer composite material.
[0019] as attached image 3 Shown is a schematic cross-sectional view of the inner layer composite material of the present invention, which is to mix waste rubber, waste sheet material particles and other additives, and then integrate them into an inner layer composite material after stirring, heating and pressing.
PUM
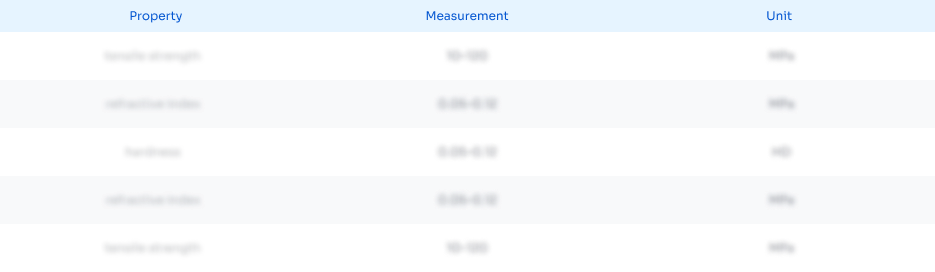
Abstract
Description
Claims
Application Information

- R&D Engineer
- R&D Manager
- IP Professional
- Industry Leading Data Capabilities
- Powerful AI technology
- Patent DNA Extraction
Browse by: Latest US Patents, China's latest patents, Technical Efficacy Thesaurus, Application Domain, Technology Topic, Popular Technical Reports.
© 2024 PatSnap. All rights reserved.Legal|Privacy policy|Modern Slavery Act Transparency Statement|Sitemap|About US| Contact US: help@patsnap.com