Solution casting apparatus and method
一种溶液、设备的技术,应用在溶液流延设备领域,能够解决干燥效率降低、湿膜破裂、膜表面劣化等问题,达到抑制干扰和、防止蒸发的效果
- Summary
- Abstract
- Description
- Claims
- Application Information
AI Technical Summary
Problems solved by technology
Method used
Image
Examples
Embodiment 1 to 11
[0093] As shown in Table 1 below, in Example 1, when the film formation was performed under the above-mentioned conditions, the gap CLs (see FIG. 5) was adjusted so that the blowing wind speed of dry air and the like from the gap CLs of the side labyrinth seal portion 75 Vs is 5 m / sec, and the gap CL2 is adjusted so that the blowing wind speed V2 of dry air or the like from the gap CL2 of the second labyrinth seal portion 62 toward the casting bead 12a is 3 m / sec. In addition, the gap CL1 is adjusted so that the blowing wind speed V1 of dry air and the like from the first labyrinth seal portion 60 is at most 5 m / sec, and the gap CL3 is adjusted so that the blowing wind speed V3 of the dry air and the like from the third labyrinth seal portion 64 is At most 5m / sec.
[0094] The blowing wind speed was measured by Anemomaster (manufactured by KANOMAX Japan Inc.).
[0095] In Examples 2 to 7, basically, the films were formed under the same conditions as in Example 1. However, in Embod...
PUM
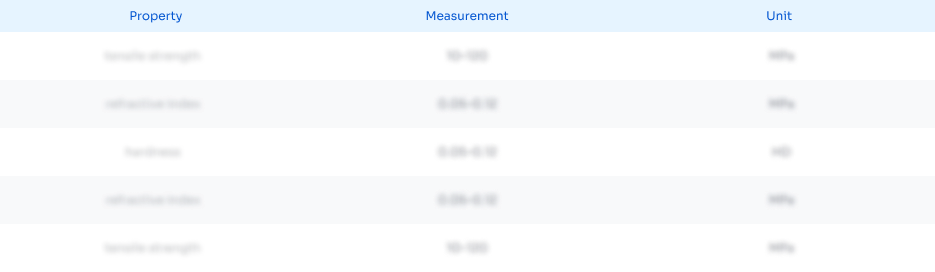
Abstract
Description
Claims
Application Information

- R&D
- Intellectual Property
- Life Sciences
- Materials
- Tech Scout
- Unparalleled Data Quality
- Higher Quality Content
- 60% Fewer Hallucinations
Browse by: Latest US Patents, China's latest patents, Technical Efficacy Thesaurus, Application Domain, Technology Topic, Popular Technical Reports.
© 2025 PatSnap. All rights reserved.Legal|Privacy policy|Modern Slavery Act Transparency Statement|Sitemap|About US| Contact US: help@patsnap.com