Stepped-flotation separation method for iron ore containing carbonas
A step-by-step flotation, iron ore technology, applied in flotation, magnetic separation, solid separation, etc., can solve the problems affecting the stability of the process, high tailing yield, large consumption of chemicals, etc., to achieve improved flotation The effect of choosing the environment and running smoothly
- Summary
- Abstract
- Description
- Claims
- Application Information
AI Technical Summary
Problems solved by technology
Method used
Image
Examples
Embodiment 1
[0030] The carbonate-containing mixed magnetic separation iron concentrate provided by Dong'anshan Sintering Plant was selected. figure 1 Process flow for flotation.
[0031] Add water to the mixed magnetic separation iron concentrate to adjust the slurry to a concentration of 20%, send the slurry to the flotation equipment, add inhibitors and stir for 4 minutes, and the addition amount is 800g / t; add collectors and stir for 4 minutes, the addition amount is 300g / t; then positive flotation is carried out to sort out siderite concentrate, and the yield of siderite concentrate is 13.31%.
[0032] Use the tailings obtained after the positive flotation process as the ore feed for reverse flotation, add NaOH aqueous solution with a pH value of 11 to adjust the slurry, and the slurry concentration is 30%; add inhibitors and stir for 4 minutes, and the addition amount is 500g / t; add activation Add collector and stir for 4 minutes, the addition amount is 1200g / t; add collector and st...
Embodiment 2
[0039] The adopted carbonate-containing mixed magnetic iron concentrate and technological process are the same as those in Example 1.
[0040] Add water to the mixed magnetic separation iron concentrate to adjust the slurry to a concentration of 30%, send the slurry to the flotation equipment, add inhibitors and stir for 4 minutes, and the addition amount is 400g / t; add collectors and stir for 4 minutes, the addition amount is 50g / t; then carry out positive flotation to sort out siderite concentrate, and the yield of siderite concentrate is 15.97%.
[0041] Use the tailings obtained after the positive flotation process as the feed for reverse flotation, add NaOH aqueous solution with a pH value of 11.5 to adjust the slurry, and the slurry concentration is 30%; add inhibitors and stir for 4 minutes, and the addition amount is 150g / t; add activation The collector is stirred for 4 minutes, and the addition amount is 600g / t; the collector is added and stirred for 4 minutes, and th...
Embodiment 3
[0051] The adopted carbonate-containing mixed magnetic iron concentrate and technological process are the same as those in Example 1.
[0052] Add water to the mixed magnetic separation iron concentrate to adjust the slurry to a concentration of 40%, send the slurry to the flotation equipment, add inhibitors and stir for 4 minutes, and the addition amount is 600g / t; add collectors and stir for 4 minutes, the addition amount is 180g / t; then carry out positive flotation to sort out siderite concentrate, and the yield of siderite concentrate is 14.26%.
[0053] Use the tailings obtained after the positive flotation process as the feed for reverse flotation, add NaOH aqueous solution with a pH value of 12 to adjust the slurry, and the slurry concentration is 30%; add inhibitors and stir for 4 minutes, and the addition amount is 300g / t; add activation Add the collector and stir for 4 minutes, the addition amount is 900g / t, add the collector and stir for 4 minutes, the addition amou...
PUM
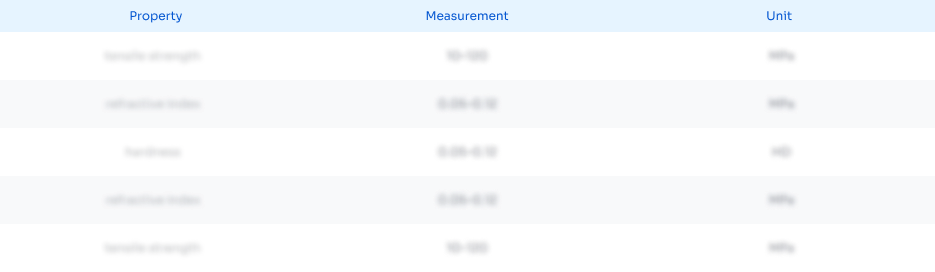
Abstract
Description
Claims
Application Information

- Generate Ideas
- Intellectual Property
- Life Sciences
- Materials
- Tech Scout
- Unparalleled Data Quality
- Higher Quality Content
- 60% Fewer Hallucinations
Browse by: Latest US Patents, China's latest patents, Technical Efficacy Thesaurus, Application Domain, Technology Topic, Popular Technical Reports.
© 2025 PatSnap. All rights reserved.Legal|Privacy policy|Modern Slavery Act Transparency Statement|Sitemap|About US| Contact US: help@patsnap.com