Grinding machine spindle end mechanism
A spindle and grinding machine technology, which is applied to the parts of grinding machine tools, grinding/polishing equipment, metal processing equipment, etc., can solve the problems of low work efficiency, cumbersome operation, and potential safety hazards, so as to reduce splash and improve the working environment Effect
- Summary
- Abstract
- Description
- Claims
- Application Information
AI Technical Summary
Problems solved by technology
Method used
Image
Examples
Embodiment Construction
[0012] Through the applicant's description of the embodiments, it will be more helpful to understand the present invention, and make the positive effects of the present invention more manifest, but the embodiments should not be regarded as limiting the solution of the present invention.
[0013] See Figure 2 and combine image 3 The spindle end mechanism of the grinding machine of the present invention includes a cone 11 arranged at the end of the spindle 1, a taper sleeve 2 with a tapered hole 21 in the middle and a thread 22 on the outer circumference, a compression nut 3, and a set plate 6 and a screw 7, the cone 11 of the main shaft 1 is provided with a square shaft keyway 112 in the radial direction of the left end surface, and a screw hole 113 is processed inwardly in the middle of the left end surface; the taper sleeve 2 is provided in the radial direction of the left end surface A square sleeve keyway 23 is provided, and a grinding wheel 5 is set on the outer circumfer...
PUM
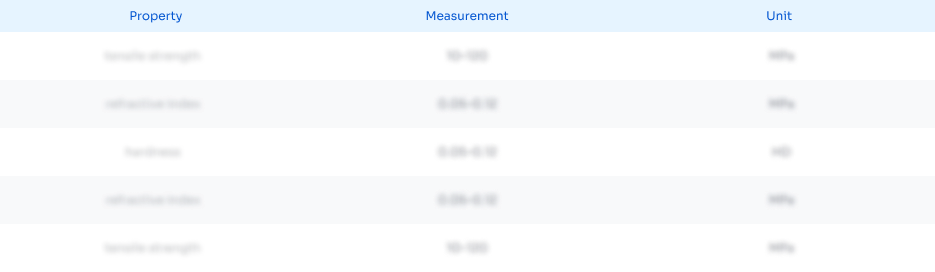
Abstract
Description
Claims
Application Information

- R&D
- Intellectual Property
- Life Sciences
- Materials
- Tech Scout
- Unparalleled Data Quality
- Higher Quality Content
- 60% Fewer Hallucinations
Browse by: Latest US Patents, China's latest patents, Technical Efficacy Thesaurus, Application Domain, Technology Topic, Popular Technical Reports.
© 2025 PatSnap. All rights reserved.Legal|Privacy policy|Modern Slavery Act Transparency Statement|Sitemap|About US| Contact US: help@patsnap.com