Hollow fiber compound film, preparation and application
A fiber composite and hollow technology, applied in chemical instruments and methods, membrane technology, semi-permeable membrane separation, etc., can solve the problems of high energy consumption, long process flow, complicated refining system, etc., and achieve simple preparation process and rich raw material sources. , the effect of high separation performance
- Summary
- Abstract
- Description
- Claims
- Application Information
AI Technical Summary
Problems solved by technology
Method used
Image
Examples
Embodiment 1
[0015] The preparation of embodiment 1 PVA-EDTMPA / PS hollow fiber composite membrane (membrane 1)
[0016] Weigh 5.0g of polyvinyl alcohol with a degree of polymerization of 1750±50 and 95g of deionized water into a three-necked flask, heat in a constant temperature water bath at 90°C, and dissolve for 1.5h while stirring at 900r / min. After completely dissolving, it is lowered to 25° C. to prepare an aqueous solution of polyvinyl alcohol with a mass concentration of 5%. Add 0.25 g of EDTMPA to the polyvinyl alcohol aqueous solution under the condition of stirring at 900 r / min, stir for 2 hours and mix evenly, filter the membrane-forming liquid through a screen to remove impurities, and then let stand for defoaming. Then the polysulfone (PS) hollow fiber support layer was soaked in the foam-free casting solution for 10 minutes, and dried at 20-25° C. for 12 hours to obtain a PVA-EDTMPA / PS hollow fiber composite membrane (membrane 1).
[0017] The prepared film 1 is subjected t...
Embodiment 2
[0018] The preparation of embodiment 2 PVA-EDTMPA / PS hollow fiber composite membrane (membrane 2)
[0019] Weigh 5.0g of polyvinyl alcohol with a degree of polymerization of 1750±50 and 95g of deionized water into a three-necked flask, heat in a constant temperature water bath at 90°C, and dissolve for 1.5h while stirring at 900r / min. After completely dissolving, it is lowered to 25° C. to prepare an aqueous solution of polyvinyl alcohol with a mass concentration of 5%. Add 0.5 g of EDTMPA to the aqueous solution of polyvinyl alcohol under stirring at 900 r / min, stir for 2 hours and mix evenly, filter the membrane-forming solution through a sieve to remove impurities, and then let stand for defoaming. Then the polysulfone (PS) hollow fiber support layer was soaked in the foam-free casting solution for 10 minutes, and dried at 20-25° C. for 12 hours to obtain a PVA-EDTMPA / PS hollow fiber composite membrane (membrane 2).
[0020] The prepared film 1 is subjected to scanning ele...
Embodiment 3
[0021] The preparation of embodiment 3 PVA-EDTMPA / PS hollow fiber composite membrane (membrane 3)
[0022] Weigh 5.0g of polyvinyl alcohol with a degree of polymerization of 1750±50 and 95g of deionized water into a three-necked flask, heat in a constant temperature water bath at 90°C, and dissolve for 1.5h while stirring at 900r / min. After completely dissolving, it is lowered to 25° C. to prepare an aqueous solution of polyvinyl alcohol with a mass concentration of 5%. Add 1.0 g of EDTMPA to the polyvinyl alcohol aqueous solution under stirring at 900 r / min, stir for 2 hours and mix evenly, filter the membrane-forming solution through a screen to remove impurities, and then let stand for defoaming. Then the polysulfone (PS) hollow fiber support layer was soaked in the foam-free casting solution for 10 minutes, and dried at 20-25° C. for 12 hours to obtain a PVA-EDTMPA / PS hollow fiber composite membrane (membrane 1).
[0023] The prepared film 1 is subjected to scanning elect...
PUM
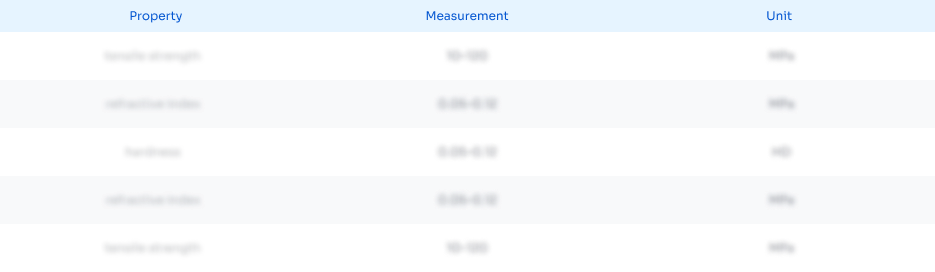
Abstract
Description
Claims
Application Information

- R&D
- Intellectual Property
- Life Sciences
- Materials
- Tech Scout
- Unparalleled Data Quality
- Higher Quality Content
- 60% Fewer Hallucinations
Browse by: Latest US Patents, China's latest patents, Technical Efficacy Thesaurus, Application Domain, Technology Topic, Popular Technical Reports.
© 2025 PatSnap. All rights reserved.Legal|Privacy policy|Modern Slavery Act Transparency Statement|Sitemap|About US| Contact US: help@patsnap.com