Method for producing porcelain basal body composite plate
A composite plate and production method technology, which is applied in the production field of ceramic matrix composite plate, can solve the problems of large energy consumption, and achieve the effects of saving energy, optimizing high energy consumption, and reducing the amount of gas generated
- Summary
- Abstract
- Description
- Claims
- Application Information
AI Technical Summary
Problems solved by technology
Method used
Examples
Embodiment 1
[0007] Example 1: Production of silver-gray composite panels with a specification of 300×900mm
[0008] The specific steps to produce this product are: 1. The raw materials required for ceramic tiles are ball milled and pressed into powder; 2. The adobes are bisque-fired at 1150°C±5°C; Achieve smooth surface and required surface area; 4. Clean up the brick adobe, and then spray paint, the weight ratio of the paint components is: polyethersulfone resin 16%, polytetrafluoroethylene 6%, titanium dioxide 3%, ultramarine blue pigment 3 %, 0.5% gold powder, 2% silver powder, 3% pearl powder, 0.05% additive, 66.45% solvent; 5. The coating is cured at 380°C for 15 minutes; 6. After curing, the product is edged and packaged in grading.
Embodiment 2
[0009] Example 2: Production of black gold composite panels with a specification of 300×450mm
[0010] The specific steps to produce this product are: 1. The raw materials required for ceramic tiles are ball milled and pressed into powder; 2. The adobes are bisque-fired at 1150°C±5°C; Achieve smooth surface and required surface area; 4. Clean up the brick adobe, and then spray paint, the weight ratio of the paint components is: polyethersulfone resin 16%, polytetrafluoroethylene 6%, titanium dioxide 1%, carbon black pigment 5 %, 1% gold powder, 1% silver powder, 3% pearl powder, 0.05% additive, 66.95% solvent; 5. The coating is cured after 15 minutes at 380°C;
PUM
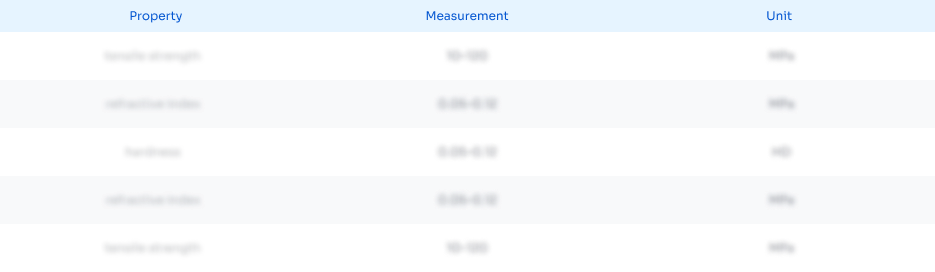
Abstract
Description
Claims
Application Information

- R&D
- Intellectual Property
- Life Sciences
- Materials
- Tech Scout
- Unparalleled Data Quality
- Higher Quality Content
- 60% Fewer Hallucinations
Browse by: Latest US Patents, China's latest patents, Technical Efficacy Thesaurus, Application Domain, Technology Topic, Popular Technical Reports.
© 2025 PatSnap. All rights reserved.Legal|Privacy policy|Modern Slavery Act Transparency Statement|Sitemap|About US| Contact US: help@patsnap.com