Ripple glaze thin film plate for oil-water separation and manufacture method thereof
A technology of oil-water separation and thin-film plates, which is applied in the preparation of corrugated thin-film plates and the field of corrugated thin-film plates, can solve the problems of high consumption in the recycling process, easy oil-stained plates, low oil-water reuse index, etc., and achieve the goal of improving removal efficiency Effect
- Summary
- Abstract
- Description
- Claims
- Application Information
AI Technical Summary
Problems solved by technology
Method used
Examples
Embodiment 1
[0017] Example 1, a corrugated film plate for oil-water separation, by weight, 72 parts of polypropylene, 14 parts of impregnated activated carbon, 10 parts of molybdenum disulfide, and 4 parts of chlorinated paraffin were evenly mixed, and then the mixture was melted at 170 ° C After filling the mold, wherein, the impregnated activated carbon is the filtration after immersing the activated carbon in 0.1 part of dilauryl thiopropionate, 0.85 part of ammonium oleate, 0.05 part of dioctyl sebacate, and 99 parts of ethanol solution for 3 hours. Dry the charcoal.
Embodiment 2
[0018] Example 2, a corrugated film plate for oil-water separation, by weight, 70 parts of polypropylene, 20 parts of impregnated activated carbon, 5 parts of molybdenum disulfide, and 5 parts of chlorinated paraffin were evenly mixed, and then the mixture was melted at 165 ° C After filling the mold, wherein, impregnated activated carbon is the filtration after impregnating activated carbon in 0.3 parts of dilauryl thiopropionate, 1.5 parts of ammonium oleate, 0.06 parts of dioctyl sebacate, and 98.14 parts of ethanol solution for 4 hours. Dry the charcoal.
Embodiment 3
[0019] Example 3, a corrugated film plate for oil-water separation, by weight, mix 80 parts of block copolymer polypropylene, 10 parts of impregnated activated carbon, 7 parts of molybdenum disulfide, and 3 parts of chlorinated paraffin, and then put the mixture at 168 ° C After hot-melting, mold filling, wherein, impregnating activated carbon is to impregnate activated carbon in 0.2 parts of dilauryl thiopropionate, 1.72 parts of ammonium oleate, 0.08 parts of dioctyl sebacate, and 98 parts of ethanol solution for 5 hours filter-dried activated carbon.
PUM
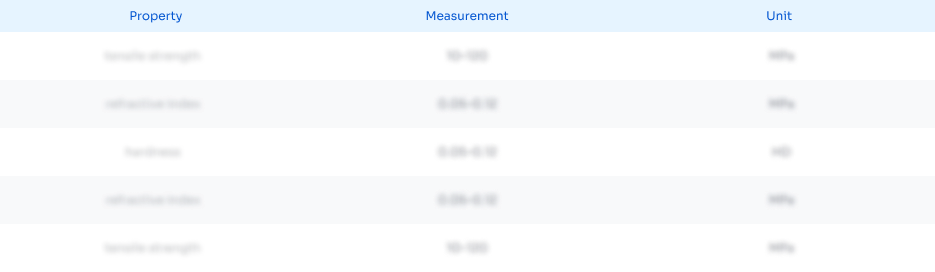
Abstract
Description
Claims
Application Information

- R&D
- Intellectual Property
- Life Sciences
- Materials
- Tech Scout
- Unparalleled Data Quality
- Higher Quality Content
- 60% Fewer Hallucinations
Browse by: Latest US Patents, China's latest patents, Technical Efficacy Thesaurus, Application Domain, Technology Topic, Popular Technical Reports.
© 2025 PatSnap. All rights reserved.Legal|Privacy policy|Modern Slavery Act Transparency Statement|Sitemap|About US| Contact US: help@patsnap.com