Real time dual bus control method for warp knitting machine
A control method and technology for warp knitting machines, which are applied in bus network, warp knitting, comprehensive factory control, etc., can solve the problems of poor reliability, stability, maintainability, inability to realize real-time control of high-speed warp knitting machines, and low manufacturing costs. question
- Summary
- Abstract
- Description
- Claims
- Application Information
AI Technical Summary
Problems solved by technology
Method used
Image
Examples
Embodiment Construction
[0016] Referring to Fig. 1, a kind of real-time double bus control method of warp knitting machine of the present invention is a kind of method utilizing network and computer control warp knitting machine, it adopts bus 1, bus 2 two buses, bus 1 adopts high-speed real-time bus , to control the operation of three warp beams 1013, 1023, 1033, a pulling shaft 1043 and a main shaft 1053, the three warp beams 1013, 1023, 1033 are respectively driven by their respective servo controllers and AC servo motors, and the warp knitting instructions are passed through The bus 1 transmits to the corresponding warp axis servo controller, the servo controller controls the rotation of the servo motor and adjusts the speed in real time according to the requirements of the instruction, and the servo motor drives the respective warp beams to ensure the yarn feeding amount of the warp beams 1013, 1023, and 1033 Meet the requirements of the pattern; the pulling command is also transmitted to the ser...
PUM
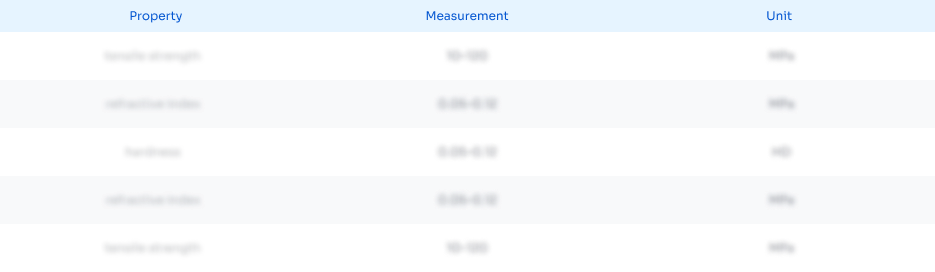
Abstract
Description
Claims
Application Information

- Generate Ideas
- Intellectual Property
- Life Sciences
- Materials
- Tech Scout
- Unparalleled Data Quality
- Higher Quality Content
- 60% Fewer Hallucinations
Browse by: Latest US Patents, China's latest patents, Technical Efficacy Thesaurus, Application Domain, Technology Topic, Popular Technical Reports.
© 2025 PatSnap. All rights reserved.Legal|Privacy policy|Modern Slavery Act Transparency Statement|Sitemap|About US| Contact US: help@patsnap.com