Dedusting dry powder recycling process
A process and dry powder technology, applied in the field of dust removal and dry dust recycling, can solve the problems of inconvenient centralized remote control, complex process flow, large equipment investment, etc., and achieve the effect of saving manpower, simplifying process flow and saving investment.
- Summary
- Abstract
- Description
- Claims
- Application Information
AI Technical Summary
Problems solved by technology
Method used
Image
Examples
Embodiment Construction
[0018] Referring to the accompanying drawings, according to a kind of dedusting dry powder recovery process flow of the present invention, it is composed of a dedusting ash bucket 1, a dust conveying device, an exhaust type dust collecting bin 9, and a wet ball machine 12 in each dedusting point of a steel plant or a metallurgical plant. It is composed of process equipment such as sealing conveying device 13, and the process equipment is simple.
[0019] This process includes three steps of dust removal ash collection, dust removal ash collection and storage, and wet ball transfer, that is, a set of dust air delivery device is installed under the dust removal hopper 1 of the dust collector, and the pressure of compressed air passes through the airtight delivery device 15 for a long distance Send it into the dust collection bin 9, and then transport it to the wet ball machine 12 through the quantitative feeder 11. After the wet ball machine 12 humidifies and pelletizes, the cond...
PUM
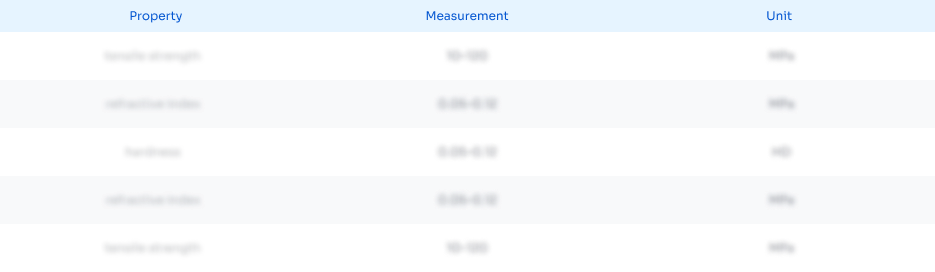
Abstract
Description
Claims
Application Information

- R&D
- Intellectual Property
- Life Sciences
- Materials
- Tech Scout
- Unparalleled Data Quality
- Higher Quality Content
- 60% Fewer Hallucinations
Browse by: Latest US Patents, China's latest patents, Technical Efficacy Thesaurus, Application Domain, Technology Topic, Popular Technical Reports.
© 2025 PatSnap. All rights reserved.Legal|Privacy policy|Modern Slavery Act Transparency Statement|Sitemap|About US| Contact US: help@patsnap.com