Ultrasonic sensor of object
An ultrasonic and sensor technology, applied in the field of ultrasonic sensors for objects, can solve problems such as high cost, uncertainty, and weak echoes that cannot be detected
- Summary
- Abstract
- Description
- Claims
- Application Information
AI Technical Summary
Problems solved by technology
Method used
Image
Examples
Embodiment Construction
[0012] Fix an ultrasonic probe 2 integrating transceiver and a "V"-shaped reflector 1 with two reflective surfaces arranged horizontally on the object. Body 1. The reflective surface is generally rectangular, smooth in itself, flat or concave or convex. A complete ranging system can include two sets of such ultrasonic sensors. The reflective surface of one set of sensors is projected in the left and right directions for measuring the left and right directions. The reflective surface of the set of sensors is projected in the front-back direction for measuring the front-back direction.
[0013] The front and rear and left and right sets of ultrasonic sensors can also share a set of post-circuits for ultrasonic ranging (including power components, operational amplifiers, etc.), so that one set works first, and the other set works later. However, a set of two-choice control circuit is required.
[0014] In some special occasions, if the object only needs to measure a set of dist...
PUM
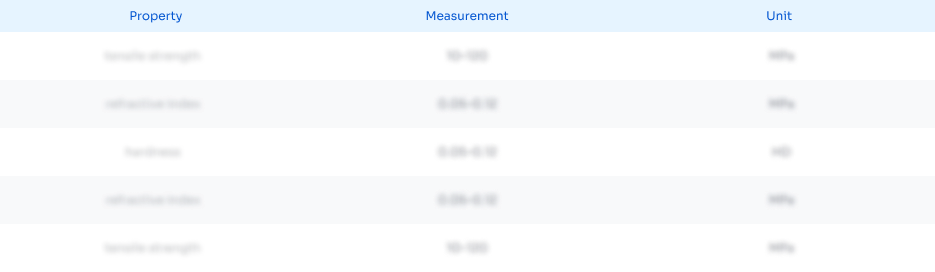
Abstract
Description
Claims
Application Information

- R&D
- Intellectual Property
- Life Sciences
- Materials
- Tech Scout
- Unparalleled Data Quality
- Higher Quality Content
- 60% Fewer Hallucinations
Browse by: Latest US Patents, China's latest patents, Technical Efficacy Thesaurus, Application Domain, Technology Topic, Popular Technical Reports.
© 2025 PatSnap. All rights reserved.Legal|Privacy policy|Modern Slavery Act Transparency Statement|Sitemap|About US| Contact US: help@patsnap.com