Electric valve
A technology of electric valves and valve shafts, which is applied in the direction of lifting valves, valve devices, valve details, etc., can solve the problems of high-priced stepping motors, large total frictional resistance, and large power consumption, and achieve device cost suppression, reduced frictional resistance, and The effect of reducing the number of parts
- Summary
- Abstract
- Description
- Claims
- Application Information
AI Technical Summary
Problems solved by technology
Method used
Image
Examples
Embodiment Construction
[0078] Next, a first embodiment of the electric valve according to the present invention will be described with reference to the drawings.
[0079] Fig. 1 shows a first embodiment of an electric valve of the present invention.
[0080] The electric valve 10 shown in FIG. 1 has a valve body 70 having a valve chamber 71 . The valve body 70 includes: a valve seat member 72 having a circular valve port 72a and a conical valve seat 72b; and a cylindrical valve with a container receiving ring shoulder 74a made by stamping. In the chamber forming member 74, the flow rate of fluid such as refrigerant is adjusted by the valve body 61 that is in contact with and separated from the valve seat 72b. The bottom surface portion with the window hole of the valve chamber forming member 74 is fixed to the valve seat member 72 by press fitting, welding, or the like. In addition, the lower end portion 40b of the bottomed cylindrical container 40 which opens downward is hermetically joined to th...
PUM
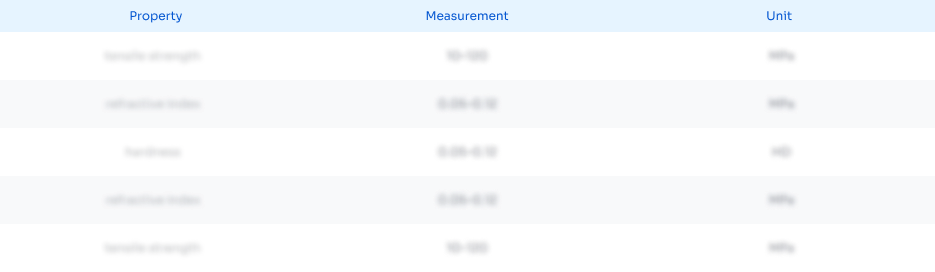
Abstract
Description
Claims
Application Information

- R&D Engineer
- R&D Manager
- IP Professional
- Industry Leading Data Capabilities
- Powerful AI technology
- Patent DNA Extraction
Browse by: Latest US Patents, China's latest patents, Technical Efficacy Thesaurus, Application Domain, Technology Topic, Popular Technical Reports.
© 2024 PatSnap. All rights reserved.Legal|Privacy policy|Modern Slavery Act Transparency Statement|Sitemap|About US| Contact US: help@patsnap.com