Automatically coiling method for overlength sheath spring
A winding method and sheath technology are applied in the field of spring manufacturing technology, which can solve the problems of high mandrel length and high mandrel winding cost, achieve uniform spring pitch, save winding spring fixtures and special tools, and spring geometric dimensional accuracy. high effect
- Summary
- Abstract
- Description
- Claims
- Application Information
AI Technical Summary
Problems solved by technology
Method used
Image
Examples
Embodiment Construction
[0011] Below in conjunction with accompanying drawing and example the patent of the present invention is further described.
[0012] Refer to Figure 1, Figure 2 and Figure 3, install the ¢2mm steel wire on the material rack of the automatic spring winding machine (model: Z53-8), pass it through the straightening roller group, the feeding roller group and the guide wire groove plate, Adjust the winding outer diameter and pitch of the spring. If it does not meet the requirements, continue to adjust various parameters until a qualified sheath spring sample is wound. After passing the inspection, the normal sheath spring winding can be started. system. After the steel wire 2 is straightened by the straightening roller 1, it is driven by the feed roller 3 to pass through the guide wire groove plate 4, and is forced to bend into a circular arc by the coil spring rod 5. The steel wire 2 is formed by two coil springs at 60° The rod 5 revolves in a helical circle around the mandrel kn...
PUM
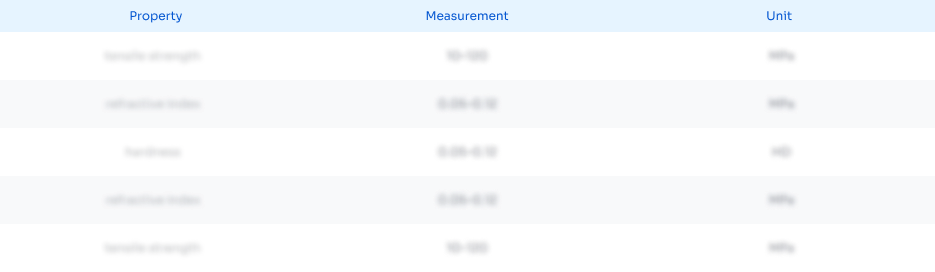
Abstract
Description
Claims
Application Information

- Generate Ideas
- Intellectual Property
- Life Sciences
- Materials
- Tech Scout
- Unparalleled Data Quality
- Higher Quality Content
- 60% Fewer Hallucinations
Browse by: Latest US Patents, China's latest patents, Technical Efficacy Thesaurus, Application Domain, Technology Topic, Popular Technical Reports.
© 2025 PatSnap. All rights reserved.Legal|Privacy policy|Modern Slavery Act Transparency Statement|Sitemap|About US| Contact US: help@patsnap.com