Thermoplastic composite structure and producing method
A composite structure and manufacturing method technology, which can be applied to other household appliances, thin material handling, cabinet/cabinet/drawer components, etc., can solve problems such as narrow gaps, faster solidification of plastic materials, and peeling off of plastic layers. Achieve the effect of avoiding insufficient filling or uneven distribution of material
- Summary
- Abstract
- Description
- Claims
- Application Information
AI Technical Summary
Problems solved by technology
Method used
Image
Examples
Embodiment 2
[0023] The plastic composite structure 20 in the second embodiment can also be formed by the above two methods.
[0024] Because there are several through holes 15 on the edge of the main body 11, the molten plastic will not only flow from one side of the side wall 14 through its edge to the other side of the side wall 14, but can reach through several through holes 15 through multiple channels. On the other side of the side wall 24 , the molten plastic will be quickly and evenly distributed on the body 11 , and the mold can be opened and taken out after cooling.
[0025] It can be understood that the main body of the plastic composite structure of the present invention can be made of hard non-metallic materials other than metal. The shape of the through hole can be a through hole of any shape, such as hexagonal, octagonal, etc., or a combination of through holes of various shapes. In addition to the horizontal setting in Embodiment 1, it can also be converted into a vertical...
PUM
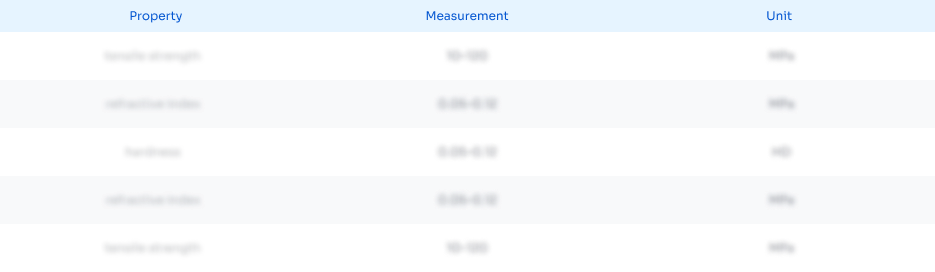
Abstract
Description
Claims
Application Information

- Generate Ideas
- Intellectual Property
- Life Sciences
- Materials
- Tech Scout
- Unparalleled Data Quality
- Higher Quality Content
- 60% Fewer Hallucinations
Browse by: Latest US Patents, China's latest patents, Technical Efficacy Thesaurus, Application Domain, Technology Topic, Popular Technical Reports.
© 2025 PatSnap. All rights reserved.Legal|Privacy policy|Modern Slavery Act Transparency Statement|Sitemap|About US| Contact US: help@patsnap.com