Workpiece transfer apparatus, control method for workpiece transfer apparatus, and press line
A conveying device and conveying control technology, which is applied in the stamping production line field, can solve problems such as control quantity variation, workpiece drop, workpiece conveying device failure, etc., and achieve the effect of suppressing vibration and preventing falling off
- Summary
- Abstract
- Description
- Claims
- Application Information
AI Technical Summary
Problems solved by technology
Method used
Image
Examples
no. 1 Embodiment approach
[0033] Hereinafter, a first embodiment of the present invention will be described with reference to the drawings.
[0034] FIG. 1 is a schematic diagram showing the configuration of a tandem press line having a phase difference control method of a workpiece conveyance device according to the first embodiment. In the figure, reference numeral A is an upstream press device, B is a downstream press device, WC is a workpiece conveying device, and P is a workpiece. Moreover, the workpiece|work conveyance apparatus WC is provided with the control part C which has the target value calculation part c1 and the servomotor driver c2, and the workpiece|work conveyance part R. In addition, in FIG. 1 , the feed (feed-out) direction of the workpiece P is defined as the X-axis, and the vertical (vertical) direction is defined as the Y-axis.
[0035]As shown in FIG. 1 , the upstream side press device A and the downstream side press device B are separated from each other with a workpiece conve...
no. 2 Embodiment approach
[0069] Next, a second embodiment of the present invention will be described. In this second embodiment, another method for calculating the target transport position will be described. In addition, since the device configuration of the second embodiment is the same as that of the first embodiment, description thereof will be omitted, and the operation of the object computing unit c1 will be mainly described below.
[0070] FIG. 6 is an operation flowchart of the target value calculation unit c1 in the second embodiment. First, as in the first embodiment, the target value calculation unit c1 obtains the upstream press angle θu from the upstream press angle detector a5, and also obtains the downstream press angle θd from the downstream press angle detector b6 (step S10).
[0071] Next, the target value computing unit c1 obtains the first coordinates (Xu, Yu)={ Fx(θu), Fy(θu)}, and by substituting the downstream side stamping angle θd+planned phase difference Δθp for the upstream...
PUM
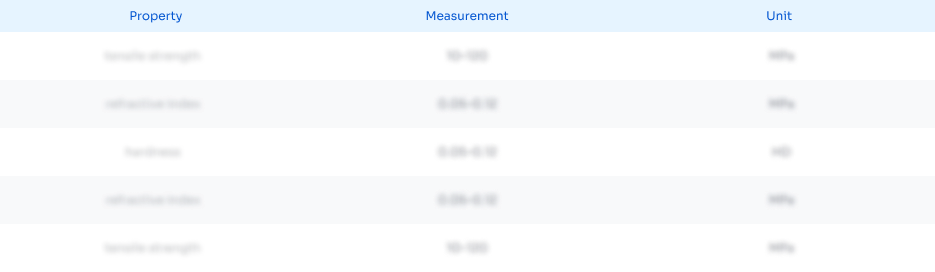
Abstract
Description
Claims
Application Information

- Generate Ideas
- Intellectual Property
- Life Sciences
- Materials
- Tech Scout
- Unparalleled Data Quality
- Higher Quality Content
- 60% Fewer Hallucinations
Browse by: Latest US Patents, China's latest patents, Technical Efficacy Thesaurus, Application Domain, Technology Topic, Popular Technical Reports.
© 2025 PatSnap. All rights reserved.Legal|Privacy policy|Modern Slavery Act Transparency Statement|Sitemap|About US| Contact US: help@patsnap.com