Florescent lamp manufacturing installation and outer electrode manufacturing method using the same
An external electrode and manufacturing method technology, applied in the field of external electrode manufacturing and fluorescent lamp manufacturing device, can solve the problems of reducing work efficiency, reducing brazing quality, uneven coating, etc., to prevent cold welding phenomenon, improve brazing quality, Simple process effect
- Summary
- Abstract
- Description
- Claims
- Application Information
AI Technical Summary
Problems solved by technology
Method used
Image
Examples
Embodiment Construction
[0050] Hereinafter, preferred embodiments of the present invention will be described in detail with reference to the accompanying drawings, and will be described within the scope that those skilled in the art can practice the present invention.
[0051] Also, the present invention can be carried out in various ways, and therefore the scope of claims of the present invention is not limited to the following examples.
[0052] 1 and 2 are schematic diagrams of the overall structure of a fluorescent lamp manufacturing device according to an embodiment of the present invention, and symbol 2 denotes a workbench.
[0053] The workbench 2 can use a conventional four-corner support with a flat work surface F on it, and when the work surface F is based on FIG. 1 , it can provide a work area that is lengthened toward the left and right.
[0054] In addition, a capping device M1 and a dipping device M2 are installed on the table 2, and are used for forming the external electrodes E on a p...
PUM
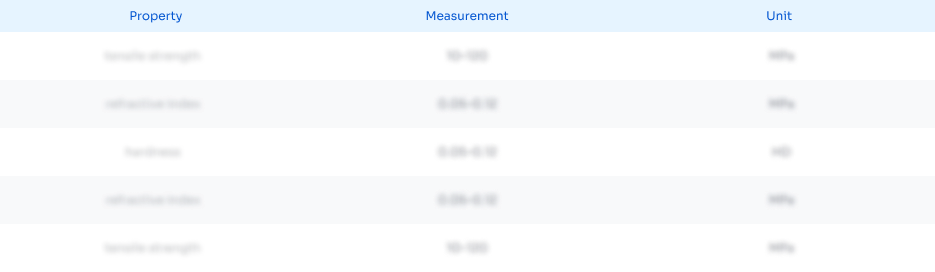
Abstract
Description
Claims
Application Information

- R&D
- Intellectual Property
- Life Sciences
- Materials
- Tech Scout
- Unparalleled Data Quality
- Higher Quality Content
- 60% Fewer Hallucinations
Browse by: Latest US Patents, China's latest patents, Technical Efficacy Thesaurus, Application Domain, Technology Topic, Popular Technical Reports.
© 2025 PatSnap. All rights reserved.Legal|Privacy policy|Modern Slavery Act Transparency Statement|Sitemap|About US| Contact US: help@patsnap.com